Integrated Molding Solutions is a one-stop shop for all of your plastic parts needs.
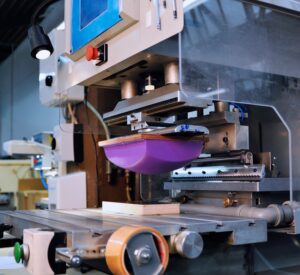
Pad Printing Services for Plastic Products
From initial plastic product design to prototyping, from injection molding to Polyjet and FDM 3D printing, and from part decorating to packaging, IMS has you covered. We perform numerous secondary processes in-house, and we partner with reputable companies for additional services. From start to finish, IMS experts add value to the plastics design, molding, and finishing processes in service to our customers. We are here to answer all your plastic questions and meet all your plastic needs.
People Also Ask
What is plastic injection molding?
Over Molding Plastic Design
Overmolding
Overmolding is a two-step plastic injection molding process in which a rigid material or substrate is molded first, then a flexible material is molded over it. Press-In Inserts
Press-in inserts are designed to be used after injection molding, when plastic is cooled and hardened.
Why chose IMS for plastic injection molding?
This question is addressed in the article above.
Where can I go to get a quick quote?
This question is addressed in the article above.
IMS offers a wide range of decorative and finishing services for plastic parts design.
Painting
Painting applies color to the part after molding. Plastic-compatible paint can be any color including metallic finishes. Painting also helps with particular requirements such as non-static parts. Some types of plastic hold paint better than others. IMS experts are here to help you with material selection to ensure your part is paintable. View one of Integrated Molding Solution’s plastic manufacturing projects that features painting.
Pad Printing
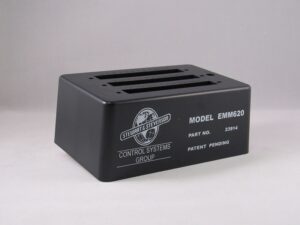
Pad Printed Plastic Part
Pad printing is another way to add color to parts. Pad printing permanently places an image onto the components. Because of its permanent nature, pad printing is ideal for plastic parts that will be handled a lot, as the color won’t wear off over time. Pad printing is similar in nature to a rubber stamp. An inverted image is coated with paint and laid against the part to transfer the image to the part’s surface. The cost for pad printing depends on the amount of colors used and the size of the image printed on the plastic part. View one of Integrated Molding Solution’s plastic parts with pad printing.
In-Mold Labeling
For this application, a label is added to the empty injection mold cavity before the molten plastic is injected. Once the plastic is injected, the label is permanently bonded to the part. This application requires specific tool design and equipment to put the label in the mold cavity, which can add some upfront costs. That added cost is often worth the price, however, as in-mold labeling is one of the most reliable methods for high-quality, consistent labeling that adheres seamlessly to the part.
Decals
If the cost of in-mold labeling isn’t in your budget, decals are the next best option. Decals are stickers that adhere to the plastic part and are a lower cost alternative to in-mold labeling. IMS sources decals for our operators or machinery to affix to the part. IMS also ensures that the decals selected have strong adhesive so they will remain on the part when the part is in use.
Electroplating
Electroplating or electro-deposition is a process whereby a metal material coats the surface of a plastic part. In the electroplating process, a permanent bond connects the metal to the surface of another piece. This process effectively coats the plastic piece in a completely shiny, smooth metal finish. Electroplating could be done for decorative or aesthetic purposes, or for a range of functional purposes. Certain materials, both plastic and metal, work best for electroplating. IMS identifies the best materials for the specific job.
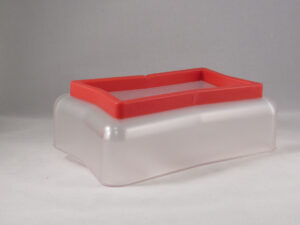
Over Molding Plastic Design
Overmolding
Overmolding is a two-step plastic injection molding process in which a rigid material or substrate is molded first, then a flexible material is molded over it. Overmolding is an additive manufacturing process that can be both decorative and functional, as it is often used for grip or for parts that require a soft-touch feel. IMS has the expertise to ensure that the plastic material in the substrate and the overmold are chemically compatible so that they bond correctly and permanently. View one of Integrated Molding Solution’s overmold designs.
IMS experts advise on plastic part design guidelines for secondary assembly processes.
Adhesives
Adhesive applications use a bonding material that chemically combines two plastic pieces for a permanent bond. Adhesives do not permit disassembly. IMS is experienced in using a number of different adhesives, such as glues and epoxies, and will advise which adhesive is the best fit for the job.
Solvent Welding
Solvent welding is a liquid solution that softens the plastic’s properties. As the solvent dries, it binds the two individual parts together permanently as one. Adhesives and solvents are often lighter, less expensive, and faster to assemble than mechanical fasteners.
Mechanical Fastening
Mechanical fasteners have the distinct advantage of offering disassembly and reassembly. Components include screws, nuts, bolts, rivets, pins, and inserts. Mechanical fasteners provide a stronger, longer-lasting bond as well as durability. When you need to ensure the strength of the hold, mechanical fasteners are often the correct choice. IMS engineers size all fasteners to ensure a perfect fit. We also work with you during the mold design phase to incorporate attachment elements like latches and hinges into the mold when possible. These elements allow the molded part to simply snap or latch together and negate the need (and the cost) for the secondary processes of adhesives or fasteners.
Tapping and Threading
Tapping and threading make for easy disassembly. Both processes produce threads, or small ridges and grooves, on a part. Tapping and threading both create threaded surfaces. The threading process makes threads on the outside surface, like a bolt or screw. Tapping creates threads inside a hole, such as a nut. Threading is performed with a die tool, while tapping requires tapping tooling. When opposite features come together, the threads interlock. View some of Integrated Molding Solution’s plastic manufacturing projects that feature tapping or threading.
UV Bonding
Ultraviolet (UV) bonding is another permanent bonding process. The ultraviolet bonding process carries the advantage of bonding plastics to other materials such as glass, ceramic, and metal. This application uses a highly intense concentration of UV light that instantly dries or cures the adhesive. UV bonding works in seconds to bond the plastic component with other materials. The speed of UV bonding lessens production time and often reduces overall cost.
Heat Staking
Heat staking is another permanent bonding technique. This bonding concept takes advantage of the base material being malleable plastic. The base material is heated up and the plastic is reformed using a combination of heat and pressure. This heated plastic is molded around the second piece forming a hardware-free bond. IMS can use heat staking to combine two alike or dissimilar materials. Also, it is a reasonably simple bonding process that does not require any additional parts or materials.
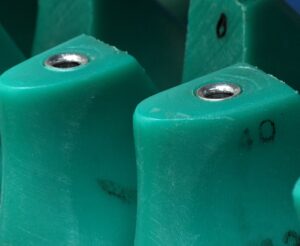
Molded In Inserts for injection molding
Molded-In Inserts
Insert molding is a systematic process of modeling thermoplastic material around an additional component. Most pliable thermoplastic resins are suitable for the insert molding process. The added pieces are often metal parts. The main advantage of molded-in inserts is that these inserts are readily available in standard sizes. Using standard-sized inserts keeps overall costs down. Metal inserts don’t wear down over time, like plastic might. View some of Integrated Molding Solution’s plastic manufacturing projects that feature molded-in inserts.
Press-In Inserts
Press-in inserts are designed to be used after injection molding, when plastic is cooled and hardened. These inserts are ideal for use in softer plastics. Press-in inserts require skilled installation to make sure there is correct tension between the plastic part and the metal insert. This type of application is cost-effective, as no special equipment or machinery is required for installation. IMS engineers are experts at designing parts for press-in inserts as well as installing the inserts.
Friction Welding
Friction welding is the process of using heat generated by friction to bond plastic pieces. There are a number of variations of this application, including linear, orbital, multi-directional, rotational, angular, and friction stir. IMS works with you on part design and manufacturing to ensure the correct friction welding application is used for the job.
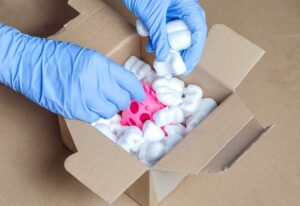
Retail Packaging for Plastic Manufacturing
IMS packages and ships plastic parts to meet your specific needs.
Retail Packaging
IMS provides retail packaging as a value-added service. Depending on the specific job requirements, IMS does blister pack assembly, barcode placement, and any other packaging needs to ensure the parts are retail-shelf ready. At IMS we cater to the customer’s needs with all aspects of the plastic design and manufacturing process, including retail packaging when needed.
Bulk Packaging
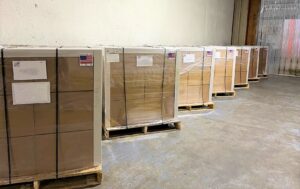
After Production Plastic Product Shipping
If you are looking for the simplest, most economical way to package your plastic product, IMS provides bulk packaging services. We make sure that your parts are protected appropriately using materials such as vacuum form trays, foam, bubble wrap, or paper inside the packaging. The cosmetic requirements of the parts dictate the amount and type of protective packaging material we use. We package mindfully so that your parts won’t get damaged in transit.
Shipping
IMS also handles all shipping needs post-process. If packages need to be under a certain weight or size, we work within those parameters. We are experienced in sizing packages to fit on all types of pallets, from standard pallets to fumigated pallets to plastic pallets. IMS handles both domestic and international shipping needs.
Contact IMS today to see how our plastic design and manufacturing process can serve you.
Customer satisfaction is one of our highest priorities at IMS. We recognize that each job is unique, and we work closely with you to ensure that we are meeting all the requirements for the specific job. The post-process services that we offer add value to the investment in your plastic parts job. IMS works with you throughout the design process to make sure your parts are designed in a cost-effective way. When and if your needs change, IMS will adapt your designs and secondary processes. The secondary processes we offer elevate the quality of your plastic parts and solidify IMS as your one-stop plastic shop.