Injection Molding
Why choose IMS for injection molding?
Integrated Molding Solutions is your number one injection molding service provider, supporting customers with professional guidance through the plastic component manufacturing process. IMS offers multiple production solutions to provide the most effective and efficient manufacturing solutions for your plastic parts. Our experience allows us to assess multiple options for most projects to ensure your products meet your form, fit, and function specifications.
Our teams experience, knowledge, and friendly customer service, make us the best plastic manufacturer in the business.
Integrated Molding Solutions offers complete plastic manufacturing services from consultation to finished product. So, whether you need a few thousand parts or a few million parts, IMS plastic injection molding gets your job done right. Trust Integrated Molding Solutions for your next injection molding project.
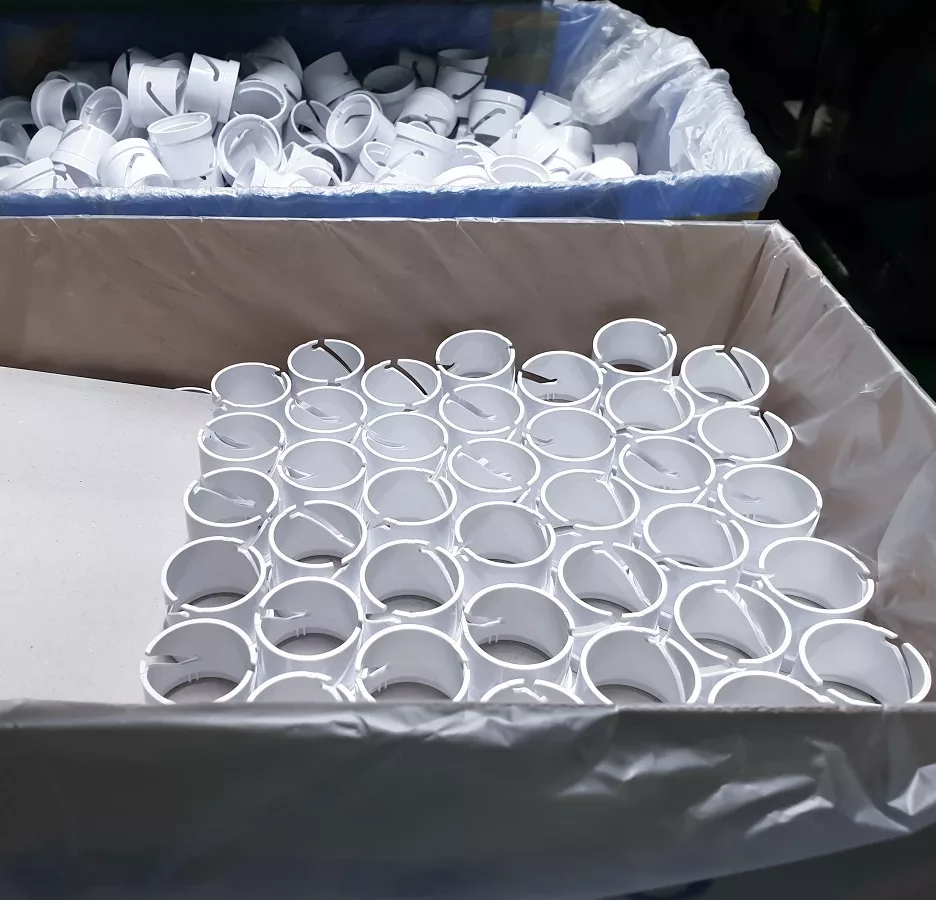
Mold Quality Safety Measures
Injection molding is a sophisticated manufacturing process.
Our professionals take added precautions to ensure only the highest quality injection molded parts leave our facility. First and foremost, IMS designs each mold with the complete process and cooling in mind. Imperfections and deformities occur when the delicate balances in the process are not optimal.
Molding engineers design the molds with sufficient cooling attributes. All design specifications incorporate temperatures and correct airflow for an ideal final product. Also, additional issues may arise if the injection molds do not have proper clamping force.
Integrated Molding Solutions provides quality control, giving the highest quality components, not excuses.
Another quality measure is to establish the correct amount of molten plastic material that is injected into the mold cavity. Inadequate injection unit levels of liquefied resin produce short shots or flash. Finally, temperature controls for each plastics’ melting point are critical. IMS’s professionalism and experience use industry standards for molten plastic flow rate, correct pressure & injection speed for precise results.
IMS artisans are veterans in the injection molding process.
Our professionals know each material, the product development process, and the science behind injection molded part making. Workers master the machines and how to use them efficiently. Regular testing and calibration of the injection molding machine are critical to the process. Testing helps to run all units smoothly and ensures outstanding parts quality. IMS continually performs quality checks on the devices as well as your products.
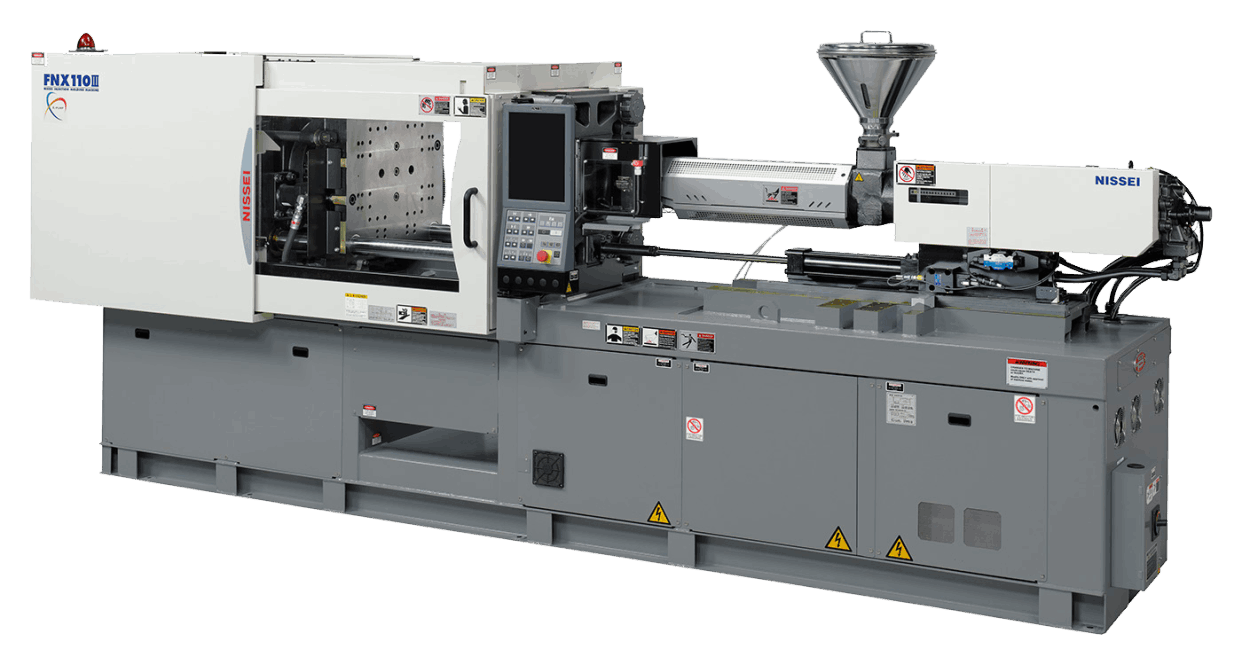
The Injection Molding Process
How do I know if injection molding is right for me?
The best way to know if injection molding is correct for your custom part is to discuss the plastic component specifics with us. But, here are some quick basics to think about. Does your product require high volume repeatability with mass production? The principal advantage of injection molding is the ability to scale fabrication in mass production with precision accuracy. Meaning large production quantities provide the same accuracy from first to last.
Likewise, the cost per piece declines with increased quantity.
Therefore, the more parts needed, the higher the cost efficiency of the manufacturing process. So, if you’re looking at thousands or millions of precision injection parts, plastics may be the right choice. Let us give you a no-obligation injection mold quote.
What if I don’t need thousands of parts?
Integrated Molding Solutions also provides 3D printing in plastics, which is often suitable for small batch processing. Integrated Molding Solutions is proud to take on small and large jobs alike. The professionals at IMS handle every job with the same quality and standards of service.
Benefits of Plastic Injection Molding
Plastic resins are known in many industries for their exceptional properties, such as lightweight, durable, and thermally insulative. With new plastic molding technology, the production processes are advancing. Further, new polymers designed for efficiency swiftly overtake their metal counterparts in parts manufacturing. Let’s see the benefits injection molding offers.
Injection molding produces plastic parts used worldwide in every industry.
Plastic injection molding creates parts ranging from micro components used in the medical industry to large pieces for automotive or industrial sectors. We use plastics every day.
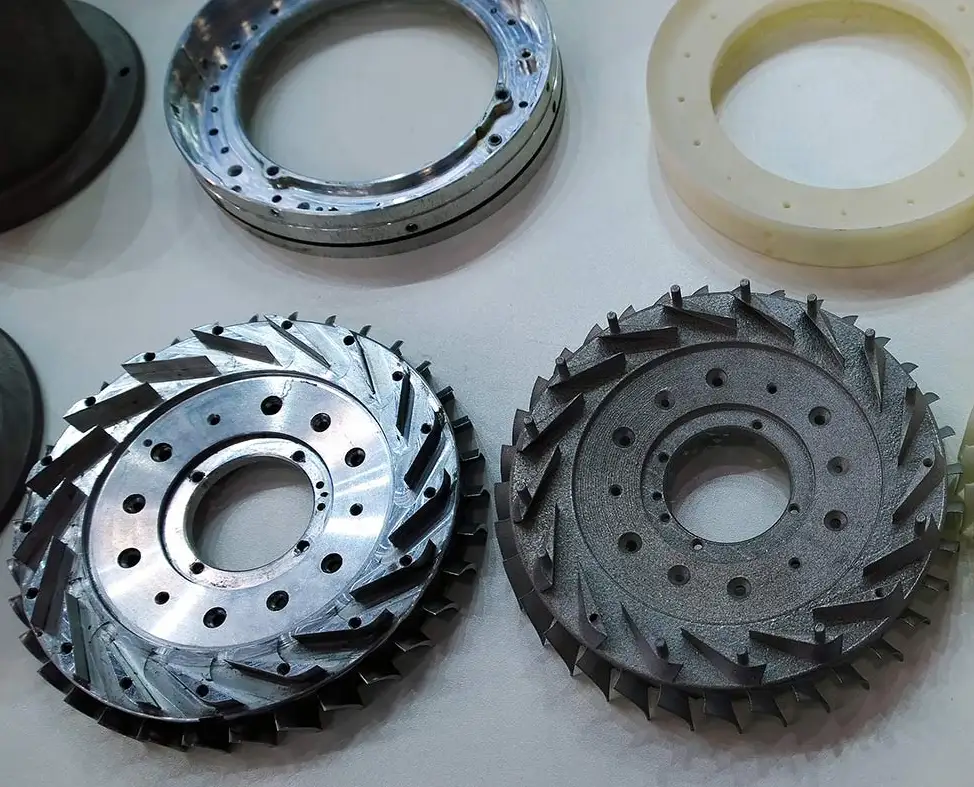
Can my metal part be made with plastic?
The top question on most business owners’ minds is, can my metal part be made with plastics? Yes, in many cases, plastics are an effective alternative. High-quality plastic injection molding makes many custom parts that were previously metal fabricated from CNC machining.
Integrated Molding Solutions is happy to discuss if moving production from metal to plastic is a beneficial solution for your parts needs. We’ll provide you with different quotes to establish multiple possible solutions and the cost-effectiveness of each. Manufacturing thousands to millions of identical injection molded parts is the strength of plastic injection molding.
What is Injection Molding?
Injection molding is the process of melting and injecting molten plastic into a custom mold which is then cooled to solidify. The plastic injection molding process produces complex shapes and geometric designs to accommodate almost any plastic parts needs.
Custom injection molding is suitable for the mass production of thousands to millions of parts.
Injection molding maintains tight tolerances for precision design specifications through thousands of reproductions. So, when you need the exact part duplicated, plastic injection molding is the production method best suited for replication without variance or processing error.
