Plastic Parts Manufacturing Capabilities
Manufacturing Repeatability in the Millions for Plastic Parts
The key benefit of manufacturing plastic parts in the injection molding process is repeatability. Integrated Molding Solutions has honed our plastic parts capabilities for over two decades. By refining their knowledge and skills to meet challenging needs, IMS is known for taking on projects that other manufacturers won’t and delivering unparalleled success.
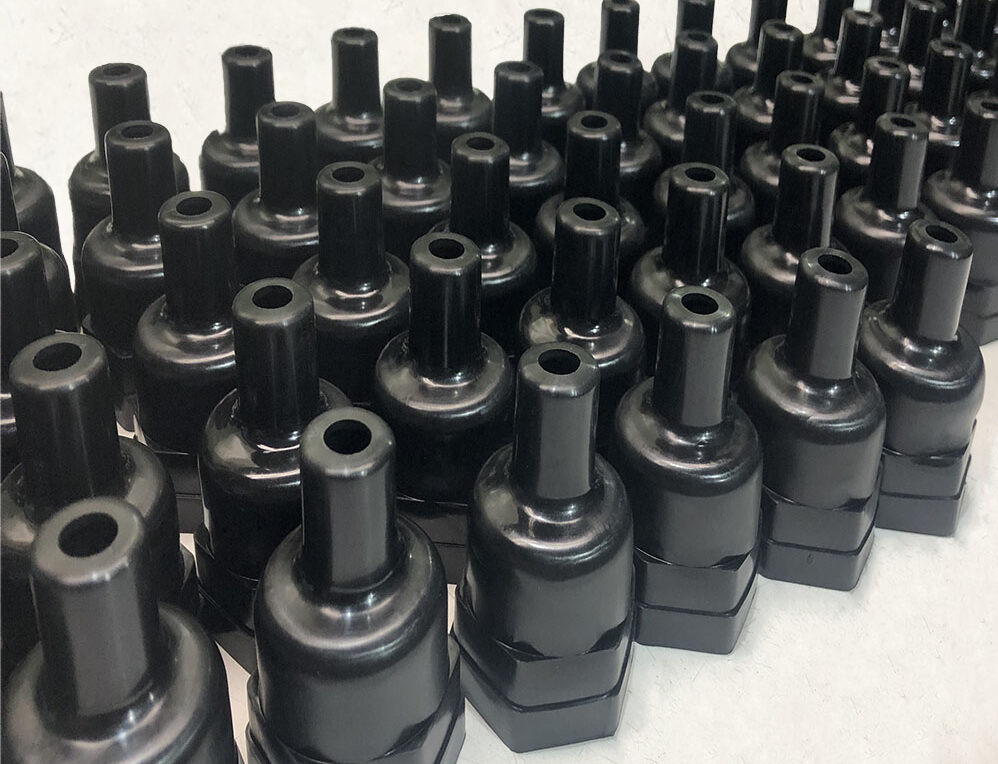
Plastic Injection Molding Services
Injection molding’s main benefit is repeatability with precision accuracy with thousands to millions of parts replications. IMS operates injection molding machines with 40 to 400 tonnage production capacity. Plastic injection molding is ideal when manufacturing large batches of detailed components. Injection molding is melting and injecting molten plastic into molds which are then cooled to solidify. Injection molding produces elaborate plastic part designs with tight variances maintained throughout batch processing.
Our experts have scientific knowledge and years of experience in injection molding techniques.
High-quality parts go through multiple quality control checks to ensure quality standards. Large production machines are calibrated for maximum efficiency and properly maintained to guarantee repeatability throughout the whole process. Molding professionals work with various materials and are well versed in the manufacturing benefits each plastic material offers. Producing 1000’s to millions of injection molding custom parts provides cost-effective plastic parts manufacturing.
Tooling For Plastic Manufacturing
Tooling is the heart of the injection molding industry. The main goal of plastic injection tooling is to design molds that retain reproducible results throughout high volume production. The tooling design process develops a strong core mold that produces perfect parts you’ll stand behind. Precision injection molding yields tooling as detailed as 0.001 variances throughout thousands to millions of pieces. Companies looking for durable complex parts and negligible variance turn to precision plastic injection molding for solutions.
Proper tooling provides a reliable process for repeat functionality.
Also, many plastic component designs often require exact specifications and precise measurements. To meet these specifications, IMS uses CAD software design. The CAD program optimizes the component within a 3D space. IMS’s preventative maintenance and rigorous inspections ensure your molds meet quality standards. IMS professionals closely follow your part’s manufacturing process from design to final usage to prevent mishaps and ensure quality standards.
3D Printed Parts & Prototypes
The benefit of 3D printing is its rapid prototyping capabilities. The medical field often requires low volume, on-demand, custom printing. 3D printing produces a detailed model from complex images such as an MRI or medical scan. Ideal for any small-batch custom 3D printing project, 3D printing is most cost-effective in small batch runs. Consider 3D printing for tasks such as prototypes, visual aids, training apparatuses, and larger-scale end-user production-ready parts. As an added value, it also delivers the end product rather quickly.
3D plastic modeling is an additive process of creating the model from the ground up.
Layering as it builds allows for intricate geometric shapes and the opportunity for a singular component. Producing a single piece eliminates multiple part costly assemblies. High-end printers deliver accuracy as close to production-grade as possible. 3D printing further provides flexibility in design changes. Design changes are relatively quick compared to time-consuming and costly changes to the tooling process or attempting to modify the end product. Confidence comes in adaptability.
Parts Assembly / Post Production Services
IMS’s postproduction and assembly services allow for flexibility and capacity for large and small jobs alike. IMS has mass production assembly line capabilities running at 300,000 pcs/month. Parts assembly is a typical secondary service. Multiple part construction is necessary to build complex pieces as one finalized component. Parts assembly consists of placing, affixing, binding, and fastening parts together to function as one piece. Assembly techniques include general assembly, heat staking, mold-in insets, adhesive bonding, tapping, thread cutting, electroplating, UV bonding, etc. Building a product using bolts, nuts, gears, bonding adhesives, and other materials maintains the part’s structural integrity to ensure it does not fail.
Parts assemblage can be as elaborate or simple as needed.
We implement design for assembly(DFA) practices to streamline all steps in the production process, including assembly. This concept realizes the complete steps in each phase and reduces unnecessary elements. Strategic planning, consolidating, and minimizing for optimal efficiency provide cost-saving opportunities.