3D Printed Parts
3D printing for plastic manufacturing parts.
When you have a small batch project of hundreds rather than thousands to millions, 3D printed parts are often an affordable solution. Professionally 3D printed parts are functional and used in many industries.
There is a cost and ROI associated with 3D printing and injection molding. Often 3D printing is cost-effective for small batch runs opposed to injection molding being cost-effective for mass production. Additionally, 3D printing usually takes the lead if your manufactured part is more significant in size. The size of a loaf of bread, for instance.
People Also Ask
What is plastic injection molding?
This question is addressed in the article above.
Why chose IMS for plastic injection molding?
This question is addressed in the article above.
Where can I go to get a quick quote?
This question is addressed in the article above.
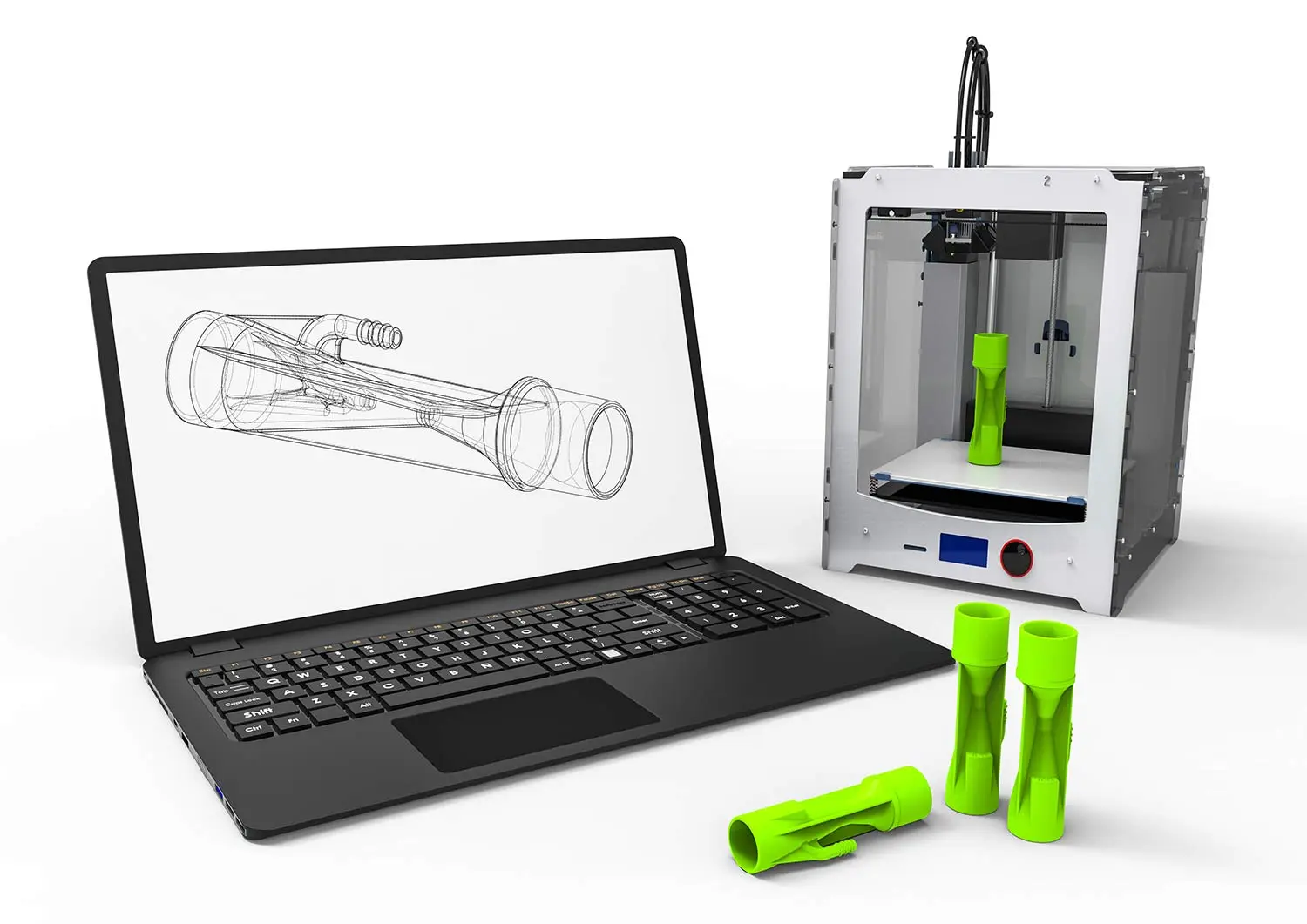
3D Printed Parts for Plastic Product Fabrication
3D printed parts have multi-color, multi-material, and versatility. The manufacturing process of 3D printing continually adds thin layers of material to construct a three-dimensional object. Get precision results from computer-aided design guidance and build your next part from scratch.
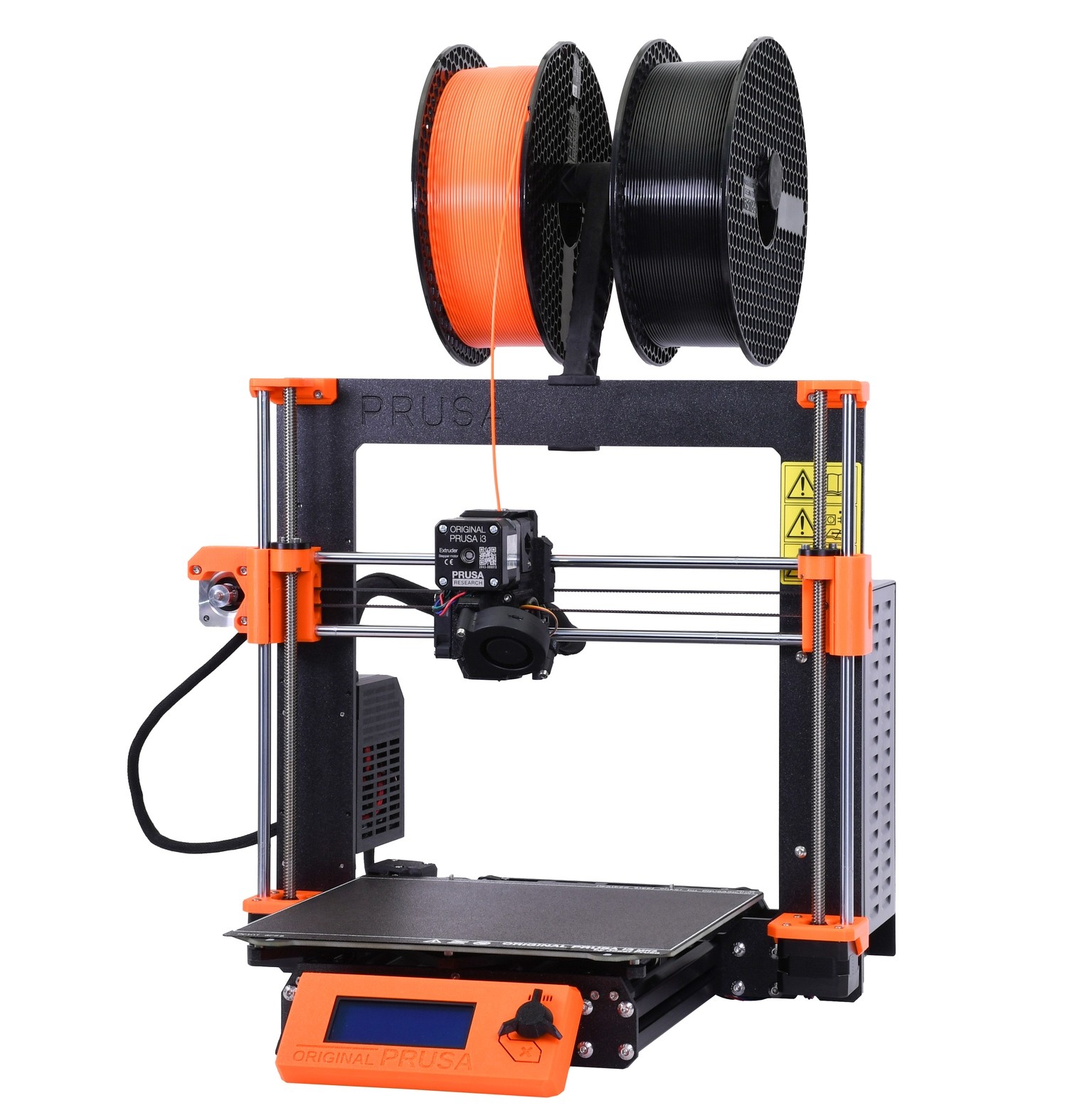
3D printing for prototyping.
3D prototypes get a three-dimensional copy of the manufactured part into the client’s hands for physical review. This way, the customers can review an actual replication of their functional part before the manufacturing process is complete. Having a sample of their finished product prior to tooling helps the design phase and builds confidence with the customer during the injection molding process and the demanding tooling phase.
Testing is important.
Early-stage prototypes are samples. Therefore, the prototype may not necessarily have all the final schematic characteristics of the finished product scheduled for injection molding production. Having design changes before tooling begins helps speed up the manufacturing process. Therefore, 3D prototypes are very efficient and effective in completing the design phase so that tooling runs smoothly.
Changing the design is far simpler and less time-consuming than changing the tooling or modifying the end product. Our skilled workers are confident and knowledgeable. Receiving a prototype helps our clients be confident in the additive manufacturing process.
Today’s technology produces Polyjet printing that achieves precision and resolution unparalleled by conventional FDM printers (fused deposition modeling). A 3D printer uses various raw materials and comes in multiple colors. Best of all, it creates mechanical properties almost identical to injection-molded parts. For precision quality, we deliver tolerances of ±0.005 millimeters.
Our PolyJet 3D printers perform consistent repeatability in the production of 3D printed parts. Capabilities of 3D printing include rigid to flexible, standard to biocompatible, and are durable to high temperatures. Further, the colors range from neutral to vibrant and opaque to translucent.
Learn about the different 3D printing options Integrated Molding Solutions offers in this plastic resource article!
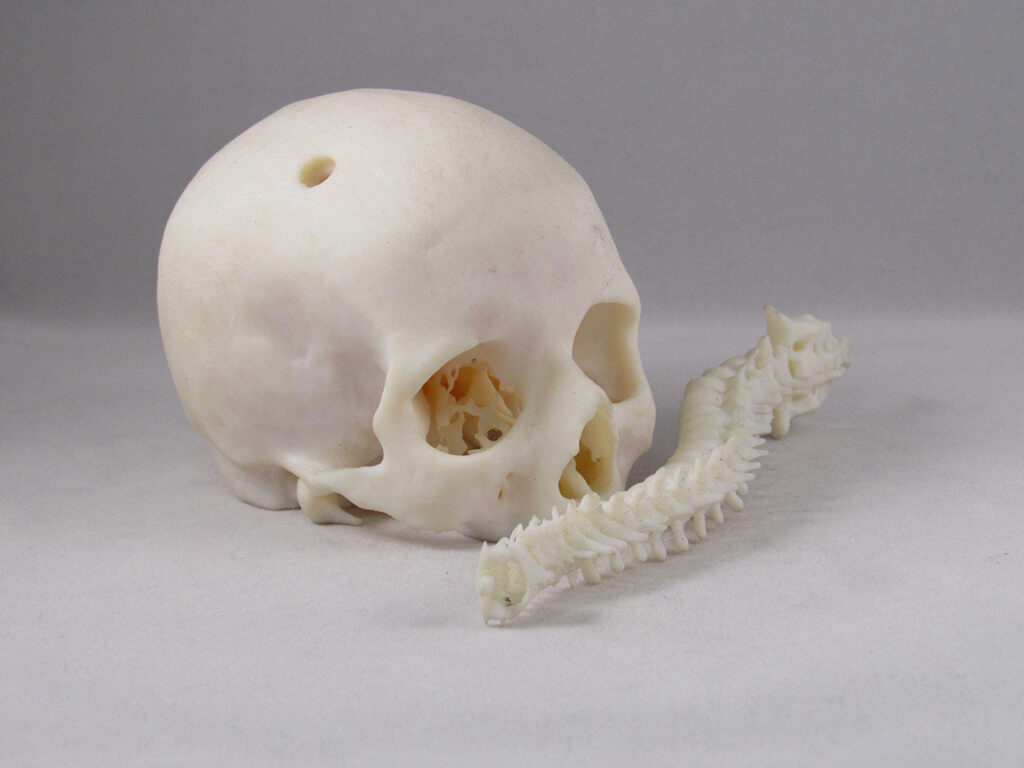
Using our 3D printing technology, our knowledgeable staff make and print 3D parts from a variety of file types.
Our artisans yield detailed models of prototype parts, consumer-ready products, and medical models taken from medical imaging. 3D printed parts also have the added value of designing the product as one whole part opposed to the assembly that injection molding may require. Each piece is different. Deciding on the correct processes is part of our expert service and years of experience. IMS guides you through the decision-making process.
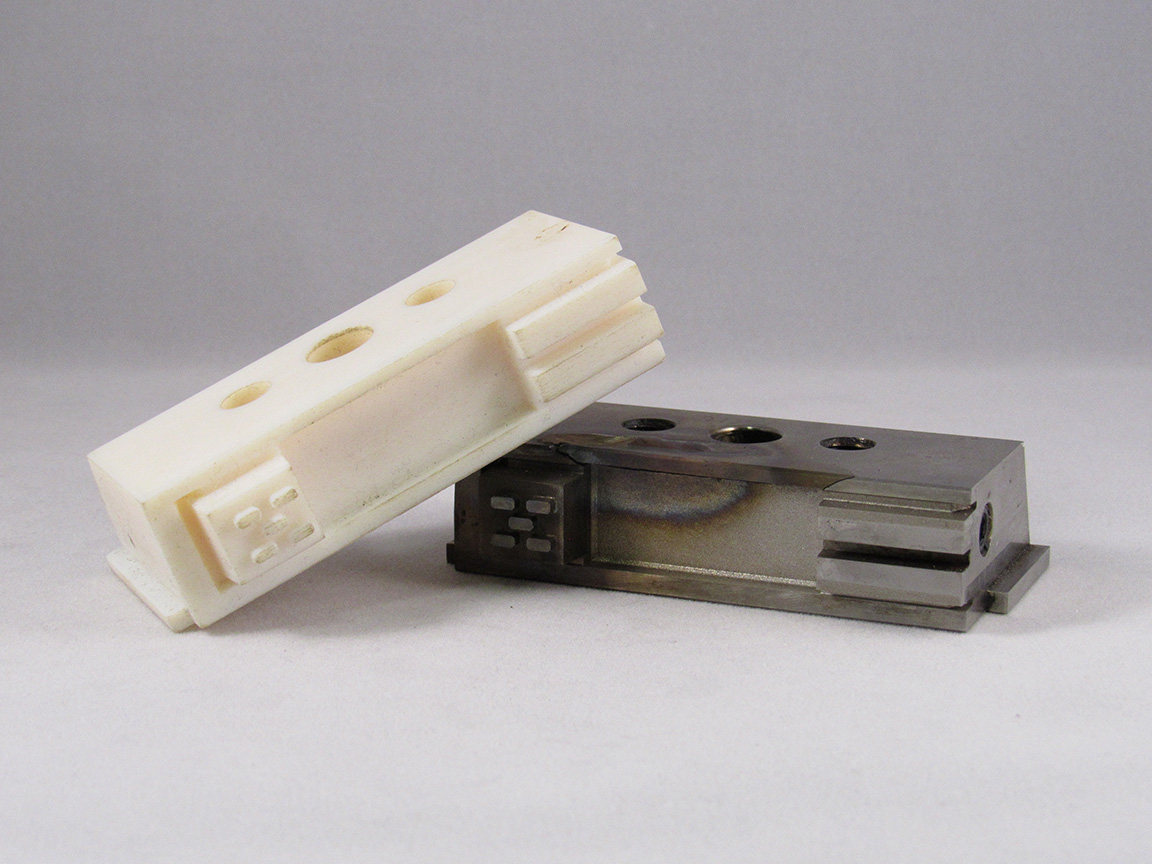
The precision quality for a 3D printed part can hold the same precise variances, intricate design geometrics, and quality trait aesthetics.
3D printing with PolyJet 3d printing can achieve high precision, custom 3D printed parts, using UV rays that pass over the photopolymer using a digital light synthesis, hardening it through a curing process. Our 3D systems achieve a high-quality surface finish as close to production-grade as possible.
What is 3D Printing?
3D printing is an additive manufacturing process. This method uses digital 3D CAD (Computer Aided Design) models and layers the 3D printing material to build physical objects. Typical 3D printing applications may include prototypes, visual aids, functional production parts, 3D molds, and jigs and fixtures for injection molding. The maximum build size Integrated Molding Solutions can prepare is 10 x 9.9 x 7.9 inches.
Building parts in thousands of thin layers permits design complexity for intricate geometric shapes.
Furthermore, 3D printing can provide internal channels or holes that traditional mills and tooling cannot reach or recreate in a singular piece. PolyJet (PJET) 3D printers use droplets of photopolymer resin to create thin layers. An ultraviolet light then passes over the thin layer of filament, curing the polymers and hardening the material, repeating the process layer after layer. Finally, when the 3D print is complete, we remove all support material used during the 3D printing process.
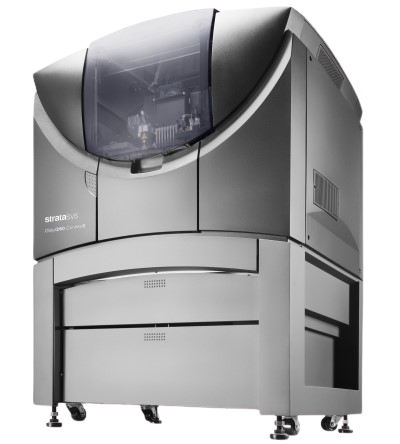
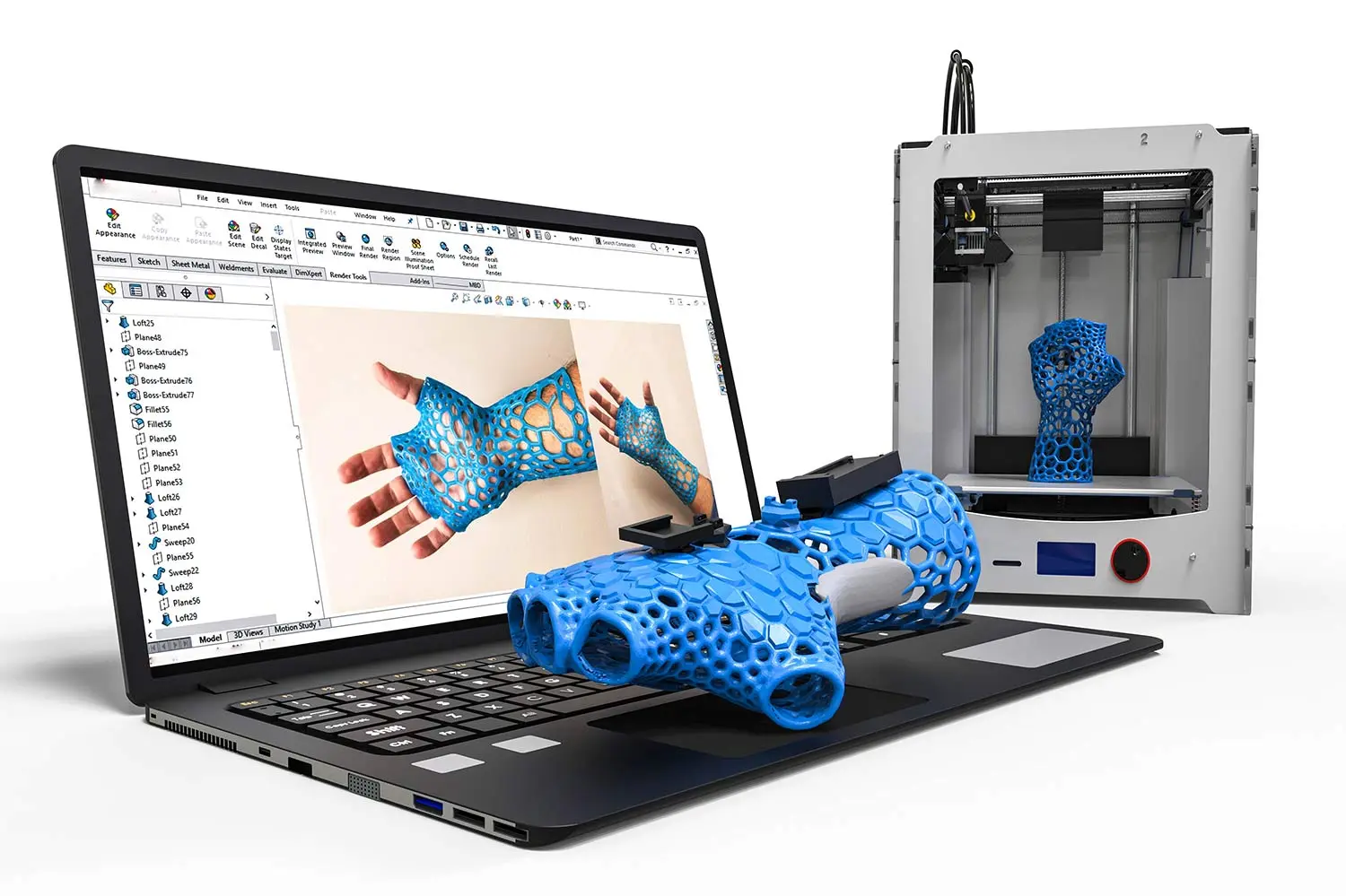
3D Printed Injection Molds
On occasion, 3D printed molds act as a cost-effective temporary limited production solution. Although steel molds are more robust and last longer, there are times that low volume production does not allow for the upfront cost of a steel mold. How do we do this? We bridge the gap between a 3D print prototype and fabricating a steel mold by producing a 3D printed plastic mold identical to a steel mold that lasts for limited production. The printed 3D insert then goes into a molding machine that molds the same part as a conventional mold at a fraction of the cost and time.
This process, for instance, is for fabrication projects such as 3D printed parts used for instruction and demonstration. Or if the project requires custom fabrication details needed in single-use. For example, a plastic model from MRI’s to be used for knee reconstruction or hip replacement surgery. In such a case, the necessary part is only applicable for this patient but still just as crucial.
3D printing advances in the medical field.
It’s a well-known fact that the medical field is continually advancing. New technologies frequently make leaps in the medical industry. Advances for 3D printing include surgical convenience, reducing surgery times, custom designs for patient comfort, and making instructional opportunities as effective and efficient as possible. Industrial 3D printing provides advances in the medical field that are endless.
PolyJet is a fast industrial 3D printing process making it ideal for on-demand customized patient-related projects.
A PolyJet 3D printer converts ultrasounds, CAT scans, and MRIs into precision 3D printed parts. The medical industry is seeing many practical uses for 3D printing. For example, a surgeon may prebend surgical plates based on the patient’s 3D model to speed up jaw surgery. The dental industry may use a 3D printed part to prepare a tooth replica for a perfect fit crown. As a result, reducing surgical time and increasing preparedness means opening larger time slots for additional patients.
The future of 3D printing for the medical industry includes such steps as replicating skin and soft tissue such as the nose or ears.
Customized 3D printed prosthetics are a low-cost solution great for kids who quickly grow out of their prosthetics. This field of study and the application for 3D printing is evolving daily. Doctors now use 3D printing to make products that match a patient’s anatomy. 3D printing also produces specifically customized prosthetic limbs for a better fit and greater comfort.
Likewise, the industry also benefits by using 3D models for patient education or counseling. A 3D-printed organ model is helpful for patient education and pre-operative planning. IMS’s 3D printing service can’t wait to jump into the future possibilities that we’ll begin exploring over the next decade.
IMS 3D Printed Parts.
At Integrated Molding Solutions, we are pioneering comprehensive solutions for 3D manufacturing. We encourage flexibility in the design and individualization of custom parts. The product you’re envisioning can come to life in 3D here at IMS. We’re proud to deliver repeatability, consistency, scalability, and design innovations in all production parts that leave our facility. Working across a wide range of industries, we bring the best 3D model components to your door.