We take sustainability seriously.
IMS is an injection molding company constantly working toward reducing our carbon footprint. We know that plastic manufacturers don’t generally have a good reputation when it comes to being environmentally friendly. But as a plastic molding company focused on eco-friendly manufacturing solutions, we continue to examine and update every step of our plastic design and production process to keep our carbon footprint as low as possible. The carbon footprint of plastic parts is measured in kilograms of CO2 per kilogram of material produced (KgCO2/Kg material).
Currently, Integrated Molding Solutions is reducing our carbon footprint in four areas:
People Also Ask
What is plastic injection molding?
IMS experts regularly use bio sourced plastic and recycled plastic for injection molding. Whenever possible, we use sustainable plastic material for injection molding.
Why chose IMS for plastic injection molding?
This is why IMS prioritizes the plastic material that has the necessary mechanical properties for the job as well as the lowest carbon footprint.
Where can I go to get a quick quote?
This question is addressed in the article above.
- Material selection
- Injection molding process and post-process services
- Injection molding equipment
- Our facility
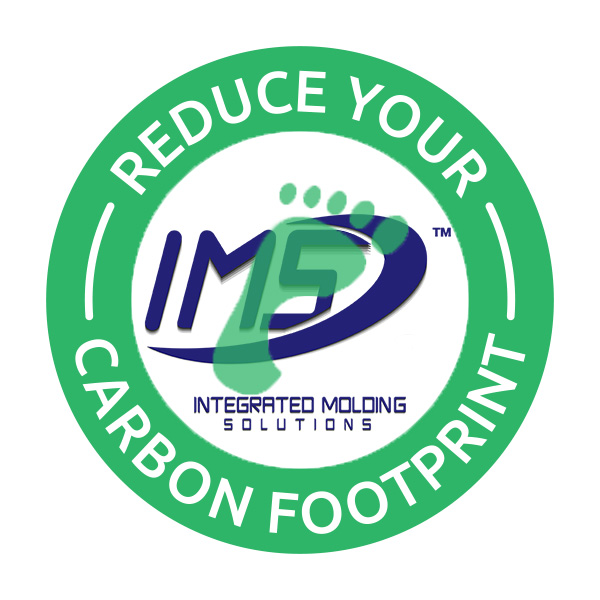
Material Selection
Consider function, form, and footprint when selecting material for your plastic part.
Selecting the right material for your plastic part is imperative. The plastic must have the mechanical properties required for part functionality, and it must have the aesthetic capabilities necessary for the form of your part. One of the biggest components of our carbon footprint comes from the materials with which we work.
Producing virgin material from hydrocarbons or crude oil comes with a significant carbon footprint. Carbon emissions from manufacturing these virgin materials are measurable before the injection molding process even begins. This is why IMS prioritizes the plastic material that has the necessary mechanical properties for the job as well as the lowest carbon footprint.
IMS experts regularly use bio sourced plastic and recycled plastic for injection molding.
Whenever possible, we use sustainable plastic material for injection molding. Bio sourced plastic, biodegradable plastic, and bio-filled plastics can utilize material made from natural sources instead of petroleum. Bio sourced plastics are significantly easier on the environment than petroleum-based plastics, as they are made from renewable resources rather than fossil fuels.
Recycled plastics are another common material choice at IMS, as they have a lower carbon footprint than brand-new plastic. We are experienced in working with PCR and PIR. Choosing recycled plastic is the quickest way to lower KgCO2/Kg material, as none of the material has to go through initial production. Recycled plastic has the same properties as the original thermoplastic resins from which it was made.
When a job necessitates petroleum-based virgin plastic, we do our best to source it locally.
Being based in Houston means we have access to domestically-produced plastic from South Texas and the Gulf Coast. First, sourcing from local areas means that we aren’t contributing to the KgCO2/Kg material with overseas transportation. Second, materials costs will also be less, which saves customers money and potentially increased revenue by completing manufacturing and getting products on shelves sooner.
Injection Molding Process and Post-Process Services
IMS engineers help you design quality parts with less plastic.
Our experts deliver quality, functional parts that are designed with simplicity and efficiency in mind. By reducing wall thickness, coring the part, and eliminating undercuts, we are able to use less material for each part, which not only saves you money, but it also significantly reduces the KgCO2/Kg material.
IMS is a plastic molding company that continually improves the energy efficiency of our plastic injection molding process.
As we work to lower our overall carbon footprint, it is important that we use less electricity to produce plastic products. In order to reduce our power consumption, we reduce cycle time. The quicker we make parts, the less energy we use. Our experienced process engineers improve the parameters of our equipment to speed up plastic injection time and cooling time.
We also tweak our molding process to reduce scrap rates. Scrap parts take energy to be molded, then energy to be ground down and re-molded, decreasing efficiency and increasing the carbon footprint of the job. At IMS we do everything in our power to get your molded product right the first time, reducing the KgCO2/Kg material and saving you time and money.
We work with local companies and package parts efficiently to ensure our post-process plastic injection molding services have the lowest possible carbon footprint.
For any post-process service we offer, we either do it in-house or work with a local partner. Our in-house post-process injection molding services include the assembly of plastic components, insert molding, packaging, and more. For services we outsource, working with local partners reduces the carbon emissions of transportation while still allowing us to offer a wider range of finishing services. Keeping post-process services local not only means that the KgCO2/Kg material is lower, but it also saves you time and money.
When we package your parts to ship to you, we do so as efficiently as possible. We are experienced in packaging your parts safely so they make it unharmed through transit while also using as little packing material as we can. Using less packing material and packaging as many parts as possible onto one pallet significantly reduces the carbon footprint of your parts.
Injection Molding Equipment
IMS uses hybrid-electric injection molding machines to deliver parts with the precision you need with a smaller carbon footprint.
There are three types of injection mold machines in the industry: hydraulic, electric, and hybrid machines Hydraulic machines are extremely precise but have higher electricity consumption. We work to be as energy-efficient as possible without compromising on the form or function of our injection molded plastic parts. To do this, we use Nissei hybrid-electric injection molding machines. The hybrid-electric machines we use at IMS give us the best of both worlds: precision and optimization along with improved efficiency. Additionally, IMS is working towards shifting the electricity that we use to power our machines and our facility to be primarily sourced from green-energy sources provided by our power company.
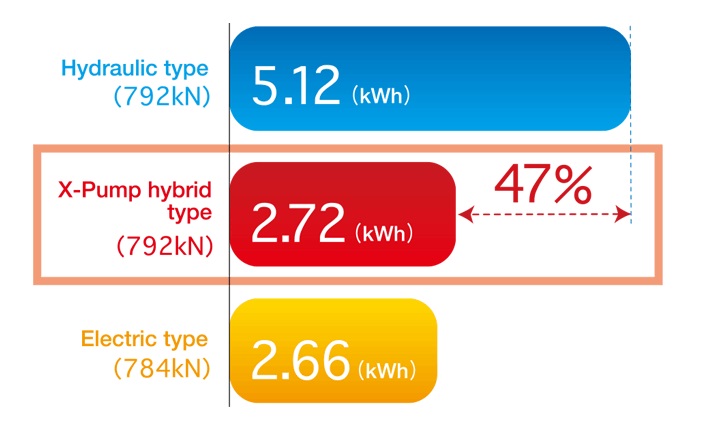
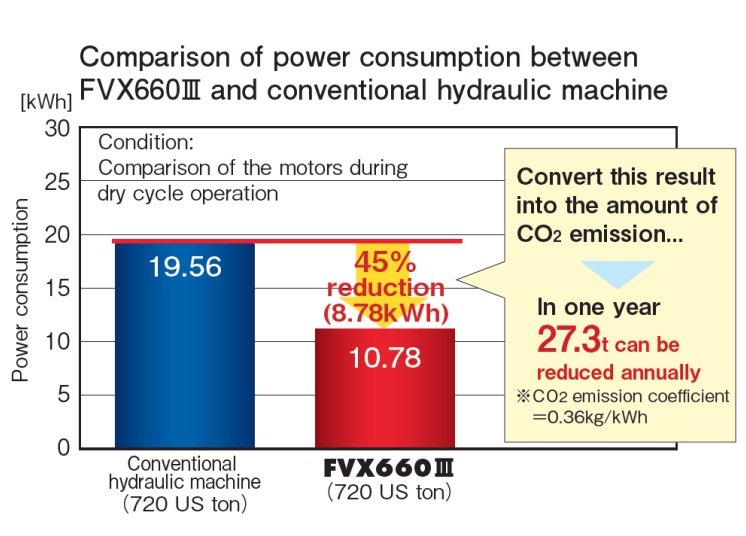
Our Plastic Molding Facility
Like many home and business owners, we have taken a hard look at how our facility can be more energy efficient as a plastic molding company in Texas.
From small changes like swapping incandescent light bulbs with LEDs and making sure our air conditioners and heating units are operating efficiently to bigger changes like investing in energy-efficient material dryers, IMS takes our carbon footprint seriously. We often use water to cool parts down, which helps reduce cycle time. To help keep our carbon footprint small, we use a closed-loop system with our water. We have our own water tower on site and use the same water over and over again.
We are partnering with IAC at Texas A&M University to identify other areas where we can improve sustainability and energy efficiency.
As part of this study A&M professionals examine our KgCO2/Kg material and advise on ways to further reduce that number. By looking at energy users such as auxiliary equipment, air compressors, dryers, lighting, and HVAC, we can improve our facility and reduce our carbon footprint. We are proud of this partnership and look forward to continuous improvement when it comes to sustainability.
If you’re a company that cares about sustainability, IMS is here for you.
Be on the lookout for a new carbon footprint line item on price quotes coming in the near future. We won’t just break down the price per part in your quote, we’ll also give you the KgCO2/Kg material so you can see for yourself exactly what the carbon footprint of your molded part will be. Have questions or other sustainability suggestions for us? Contact IMS, your local plastic molding company today!
Integrated Molding Solutions delivers high-quality parts with a low carbon footprint.
When it comes to sustainable practices, we are working hard to learn and implement all we can. We know you are, too. Let’s learn and improve together while also meeting all of your custom injection molding needs. Contact us today to start the injection molding process.