Types of Sustainable Plastic Materials for Plastic Product Fabrication.
Prior to the development of sustainable plastics, traditional plastics were sourced exclusively from fossil fuels. In the traditional plastic production process, fossil fuel is broken down into polymers and made into virgin material with specific mechanical properties needed for any given plastic application. While virgin plastic is still important to achieving certain precise mechanical properties, the plastics industry is working towards sustainable development in plastic production in order to avoid mounting plastic waste and plastic pollution, particularly from single-use plastic. As the plastics industry aims to reduce its carbon footprint, four types of sustainable plastic have emerged as frontrunners for their use in a wide range of applications. Bio sourced plastic, biodegradable plastic, recycled plastic, and renewable plastic are all environmentally-conscious, sustainable plastic choices that have many of the same capabilities as conventional plastic. Integrated Molding Solutions is here to help you meet your plastic sustainability goals.
People Also Ask
What is plastic injection molding?
Plastic parts that are scrapped during production and unused plastic portions from the injection molding process are reground and used again. In addition to the sustainable nature of PIR, another benefit is that the plastic manufacturer knows exactly what the recycled material is and what its properties are, as the supply chain is a closed loop.
Why chose IMS for plastic injection molding?
This question is addressed in the article above.
Where can I go to get a quick quote?
This question is addressed in the article above.
Bio Sourced Plastic
For consumer products or parts that have loose requirements for mechanical properties, bio sourced plastic is often the best sustainable plastic choice. The polymers that form bio sourced plastics are derived from plants instead of petroleum. Starch, a natural polymer, is taken from plants like potatoes, beets, and corn for use in bio sourced plastics. Lignin, the polymer which composes wood, can also be used in this type of sustainable plastic.
Bio sourced plastics have applications in a number of products that do not have strict requirements for mechanical properties.
For example, bio sourced material works well for plastic packaging and plastic bags. The performance window of bio sourced plastic is limited as there are currently only two grades available: polylactic acid (PLA) and polyhydroxyalkanoates (PHA). Of these two bio sourced plastics, PLA is more widespread. PLA, commonly made from corn or sugarcane polymers, has a range of applications beyond sustainable plastic packaging. It is a common filament grade for FDM 3D printers and is used widely in 3D printed prototypes. PLA is also used to make plastic bottles, food packaging, and some medical devices. PLA is a cost-effective bio sourced plastic option for sustainable plastic products.
PHA, on the other hand, is currently less widespread, making it less cost-effective. While it has similar applications and mechanical properties to PLA, PHA is made using an entirely different type of biological, renewable material. PHAs are polyesters that are created by bacteria as part of the bacteria’s digestion process. While the technology is not quite there yet, PHA certainly promises to be a cost-effective option for bio sourced plastic in the future. As PHA is more biodegradable than PLA, it is also a good option for medical devices like screws, rods, or plates that need to dissolve within the human body over a set period of time.
It is important to note that while bio sourced plastics are sourced from renewable materials, they are only biodegradable in specific environments if at all.
PLA can biodegrade under certain temperatures and light conditions typically found only in industrial composting facilities. PHA biodegrades in a much wider range of environments, including marine and soil. Also important to note is that neither PLA nor PHA can be recycled by traditional means alongside other material streams. Both need to be sent to specialty waste management plants or industrial composting facilities to be properly recycled.
Biodegradable Plastic
It can take traditional plastic hundreds to thousands of years to fully degrade. Biodegradable plastics decompose in a much quicker timeframe under the right conditions. Biodegradable plastics are designed to break down in the presence of heat, moisture, oxygen, and/or light. These sustainable plastics have a narrow performance profile because of their limited mechanical properties. They are, however, an excellent choice for plastic bags and plastic film, both of which are major contributors to the planet’s landfill problems. Working towards packaging sustainability is a critical goal in tackling our society’s single-use plastic problem.
There are several commonly used grades of biodegradable plastic, including polybutylene adipate terephthalate (PBAT), polybutylene succinate (PBS), and polycaprolactone (PCL).
PBAT is a biodegradable plastic that breaks down in soil in about six weeks, making it a great choice for compostable plastic packaging. Unlike bio-sourced plastics, however, PBAT is derived from fossil fuels. PBS is another widely used grade of biodegradable plastic. PBS can be derived from either fossil fuel or renewable resources like fermented glucose, making it an even more environmentally-friendly choice than PBAT. PBS biodegrades almost fully within 70-100 days. PCL is a third grade of biodegradable plastic with a number of applications in the medical industry. PCL stands out from PBAT and PBS because of its unique mechanical properties. PCL is moldable and putty-like when warm. It biodegrades within two to three years in the right conditions.
Biofilled plastics are another type of biodegradable, sustainable plastic.
Biofilled plastic is generally standard petroleum based plastic (though it can be plant-based) that incorporates an organic, sustainable material as a filler. Coconut husks, rice hulls, and industrial hemp are all commonly used biofiller. Biofiller not only helps reduce reliance on fossil fuels for plastics manufacturing, but also improves mechanical performance. The filler adds strength to the plastic and has the benefit of being renewable. Biofilled plastics degrade at different rates based on the particular biofiller used.
Recycled Plastics
There are three primary categories of recycled plastics: post consumer recyclables (PCR), post industrial recyclables (PIR), and depolymerization.
PCR material is the type of recycled plastic that likely comes to mind for a consumer.
Plastics that have already been used for their original purpose are collected by a recycling center, sorted, cleaned, and ground down. This plastic material is then available for reuse within a closed loop or circular economy. The circular economy of PCR means that plastics which have already been produced are reused, potentially numerous times, thus reducing the need for the production of new petroleum based plastic. This in turn reduces carbon dioxide and greenhouse gas emissions caused by plastics manufacturing. While the PCR circular economy certainly benefits the environment, it comes with the downside of material degradation. When plastic is heated, broken down, reheated, and broken down over and over again, it loses certain mechanical properties. If desired, IMS engineers will work with you to ensure that your project incorporates as much sustainable PCR plastic as possible while still maintaining full functionality.
PIR material is an even smaller closed loop.
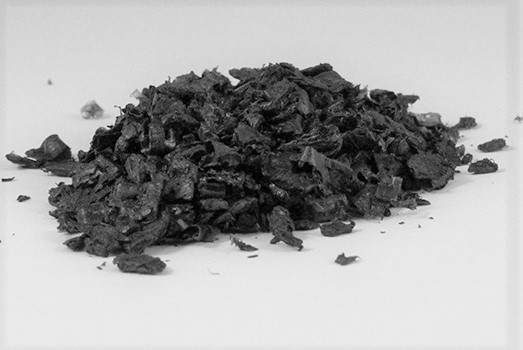
PIR (regrind) Plastic Material Example
PIR material, also known as regrind, usually comes from within a plastics manufacturing molding facility. PIR is essentially internal plastic recycling within a plastics manufacturing plant. Plastic parts that are scrapped during production and unused plastic portions from the injection molding process are reground and used again. While IMS technicians design injection molds so that they do not waste plastic, some unused parts like gates and runners are unavoidable. In addition to the sustainable nature of PIR, another benefit is that the plastic manufacturer knows exactly what the recycled material is and what its properties are, as the supply chain is a closed loop. At IMS we are able to successfully make many consumer-grade parts with 100% PIR. For more technical parts, IMS experts provide guidance on recycled content percentages to guarantee both performance and sustainability.
Depolymerization utilizes either PCR or PIR material.
Rather than mechanically grinding down the recycled plastic, depolymerization uses chemicals and heat to break down plastic polymers into monomers. These monomers are then used as replacement feedstock, or raw material, in the polymerization process when plastic material is made. Again, this recycling method significantly reduces reliance on fossil fuels. Rather than using fossil fuels to make plastic monomers, these monomers are sourced from pre-existing plastics. Another benefit of depolymerization is that its mechanical properties mimic that of virgin plastic. Depolymerization is a newer technology, however, and therefore is not yet as cost-effective as PCR or PIR.
Renewable Plastic
Renewable plastic goes another step beyond depolymerization. Renewable plastics use renewable feedstock during the polymerization process. The plastic is produced in the exact same way as virgin plastic. The difference is that instead of using petroleum based raw material, renewable plastic uses renewable raw material derived from hydrocarbons in natural fats, natural oils, and waste. While depolymerization breaks down polymers from recycled plastics into monomers, renewable plastics actually use chemicals from sustainable resources to form those monomers. Renewable plastic mimics the mechanical properties and functionality of traditional plastic, making it a sound choice for more technical parts.
Contact IMS today to see how we can help you meet your sustainability goals.
IMS experts work with you to determine the type of sustainable plastic that is the best fit for your project and budget. If you have a request for a specific amount or percentage of recycled material used in your plastic part, IMS will find a way to deliver on both sustainability and functionality. We can even include a small marker or label on your product alerting the consumer that it is made from recycled or sustainable plastic. Sustainability is important to us at IMS, and we strive to find the best, sustainable solutions for all our customers’ needs.