When manufacturing plastic parts with injection molding, ensuring cycle times are optimized is critical for increasing efficiency and keeping costs low.
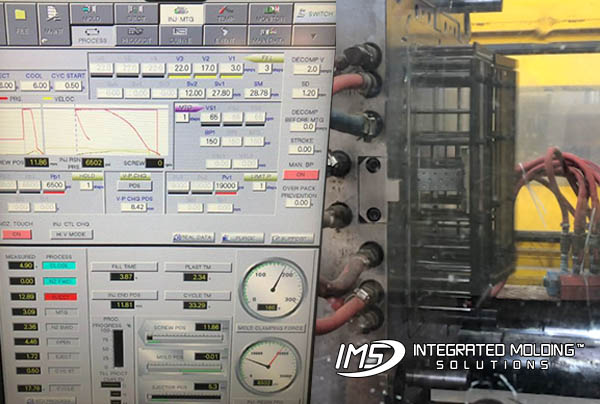
Cycle time refers to the throughput time for an injection molding machine to complete a full cycle of injection, holding, cooling, and ejection. The machine cycle wields significant influence over both the plastic manufacturer’s production process and the customer’s supply chain and margins. This article looks at the importance of calculating cycle time precisely, its use in product development, and how an optimized cycle time formula can improve the injection molding, manufacturing process.
The Crucial Role of Injection Molding Cycle Time:
Cycle time is a critical factor for keeping costs and lead times down for injection molding. As a core definition, it encapsulates the entire span of injection molding – from the moment molten plastic is injected into the mold to the instant the molded part is ejected, ready for subsequent stages. Calculating cycle time for injection molding is done by timing from one part ejection to the next part ejection. Manufacturing cycle time is important for keeping lead time low, serving as a determinant of production capacity, cost-effectiveness, and overall manufacturing efficiency. Lowering cycle time will also have a positive impact on takt time.
The Importance of Cycle Time in Production:
At its core, cycle time embodies a direct correlation with production capacity. The more effective cycle time is, the more parts a molding machine can churn out within a given production schedule, be it a shift, a day, or a month. Lower production time arises from reduced cycle times, enabling manufacturers to meet high-volume customer demand for multiple parts without compromising on quality.
Optimization Strategies for an Effective Cycle Time:
Strategic Part and Mold Design:
Cycle time optimization begins at product development and mold design. The thinner the wall thickness is in your mold, the faster your part or product solidifies. This shortened cooling reduces the actual cycle time. So, the more you reduce wall thickness while, preserving structural integrity, the quicker the processing time from injection to ejection.
Efficient Cooling Mechanisms:
Your cycle time is greatly impacted by the effectiveness of cooling built into your mold. Besides wall thickness, there are other methods for pulling the heat away from the cavity. These include having multiple water lines, that are strategically placed. These water lines will keep thermally managed water constantly running through the mold, therefore reducing the average cycle time.
Plastic Molding Materials Selection Matters:
The choice of plastic material and its intrinsic properties significantly impact cycle time. Materials with lower melt temperatures will cool quickly, resulting in a shorter total cycle time. Injection Molding Materials also differ in heat capacity and viscosity. Materials with lower heat capacity and lower flow viscosity tend to fill the cavity quicker in the injection processes, which also will reduce your total cycle time.
New 3D Printing Cooling Technology:
Innovations such as conformal cooling, involving the 3D printing of molds to align with part geometry, are revolutionizing cycle time reduction. This sophisticated approach enhances heat extraction and, subsequently, accelerates cycle times.
Injection Mold Material Selection:
The heat capacity of mold materials, often steel or aluminum, is another influential element. The selection of materials with optimal heat capacity enhances heat transfer efficiency and contributes to shorter cycle times. Steel, aluminum, or other metals / materials will hold heat in different ways. Therefore, the material your injection mold is made from will affect how quickly the mold cools, and reduce the total time for the plastic product to be ready for ejection.
Cycle time calculation is an essential element in the manufacturing process of plastic parts through injection molding.
Calculating and reducing cycle times play a large role in cost and total time of production. Factors including plastic part design, overall equipment effectiveness, cooling mechanisms, material selection, and mold design, are crucial to optimize cycle times. If done correctly, you will see heightened productivity, reduced costs, and elevated customer satisfaction. As the plastic molding industry continues its evolution, the pursuit of shorter cycle times remains a vital pursuit, embodying the quest for operational excellence and continuous improvement.
Count on molding experts like Integrated Molding Solutions to take every consideration to minimize your injection molding cycle times.
As the plastic molding industry continues to evolve, the pursuit of shorter cycle times remains a vital pursuit. Reach out to the experts at Integrated Molding Solutions for any questions on cycle times and to see if we can optimize or reduce yours.