Glass filled plastic has emerged as a versatile material, widely used across industries where enhanced mechanical properties are essential. But what exactly is glass filled plastic, and why is it a popular choice? In this article, we’ll explore the pros and cons of it, delve into its applications, and compare it to other filled plastics.
What is Glass Filled Plastic (GFP)?
Glass filled plastic is a composite material where plastic resin is reinforced with glass fibers similar to how concrete might be reinforced with rebar. This combination of plastic and glass significantly improves the rigidity of the material and enhances key mechanical properties, including tensile strength, shear strength, thermal stability, and wear resistance. One of the standout benefits of glass is its chemical resistance, as glass is inherently inert.
People Also Ask
What is plastic injection molding?
But what exactly is glass filled plastic, and why is it a popular choice? What is Glass Filled Plastic (GFP)?
Why chose IMS for plastic injection molding?
This question is addressed in the article above.
Where can I go to get a quick quote?
This question is addressed in the article above.
As with any injection molded part, it is critical to go through the engineering design process to ensure that parts are molded defect-free. IMS specializes in this process, providing part designs that meet all specifications and are ideal for injection molding.
How is Glass Filled Plastic Different from Fiber Reinforced Plastic?
In contrast, fiber reinforced plastic (FRP) is a broader category of composites that can use various fibers (glass, carbon, aramid) embedded in a thermoset resin, often with continuous or woven fibers for higher tensile strength and performance.
Glass Filled Nylon Plastic and Other Resin Options
Nylon material and other various plastic materials can be used as the base material in glass plastic, each offering different properties:
- Nylon (Polyamide): Commonly used for its high strength, wear resistance, and thermal stability. Ideal for automotive and industrial applications.
- Polypropylene: A lightweight and cost-effective option, offering good chemical resistance and moderate strength, often used in consumer goods and packaging.
- PBT (Polybutylene Terephthalate): Known for its excellent electrical properties, PBT is used in electronics and automotive parts that require good dimensional stability.
- ABS (Acrylonitrile Butadiene Styrene): Offers a balance of toughness, rigidity, and ease of molding, often used in household appliances and automotive interiors.
These resins, when combined with glass fibers, improve the mechanical properties of the final product to meet specific application needs.
The Benefits of GFP
- Improved Strength and Rigidity: The addition of glass fibers to plastic enhances its structural integrity. This is particularly important in applications where parts are subjected to high stress, as the material’s rigidity ensures better performance.
- Enhanced Thermal Stability: GFP’s exhibits superior thermal stability, making it suitable for environments with fluctuating temperatures. The material can maintain its shape and performance even under high heat.
- Reduced Sink in Molding: During the molding process, glass filled plastic remains solid throughout, reducing the occurrence of sink marks. This results in parts with better surface quality and dimensional accuracy.
- Increased Fatigue Life: Parts made from GFP’s demonstrate increased fatigue life, meaning they can withstand repeated stress over time without deforming or breaking.
- Chemical Resistance: Thanks to the inert nature of glass, GFP’s are highly resistant to chemicals, making it ideal for use in harsh environments where chemical exposure is a concern.
Drawbacks of Glass Filled Plastic
While glass plastics offers numerous advantages, there are some drawbacks to consider:
- Brittleness: Depending on the fill percentage, it can become more brittle, making it susceptible to cracking under high impact. The engineers at IMS will help you determine what fill percentage is appropriate for your application.
- Aesthetic Challenges: High fill percentages can impact the appearance of the finished part, with glass fibers sometimes visible on the surface. However, careful design, engineering, and plastic color choices can mitigate this issue.
- Warpage: Glass fibers align in the direction of flow during molding, which can lead to non-linear shrinkage. This can cause warping in the final part, which requires careful consideration during the design process. IMS engineers work diligently during the design phase to ensure minimal warpage.
- Increased Wear on Molds: The abrasive nature of glass filled plastic can lead to increased wear on injection molds, necessitating the use of harder tool steel. This can also increase wear on other components of the injection molding machine, such as the screw and barrel.
Alternatives to Glass Filled Plastic
While GFP’s are a popular choice, other filled plastics have different benefits and drawbacks:
Plastic Type | Benefits | Drawbacks |
Carbon Filled Plastic | Carbon fibers or carbon powder can be used to reinforce plastic, offering even greater strength and stiffness than glass. Carbon filled plastics also provide electrostatic discharge protection, making them useful in applications requiring conductivity. | Carbon filled plastic is more expensive and typically available in fewer material types. |
Natural Organic Fillers | Fillers like wood, hemp, and pecan shells offer a sustainable alternative. They are biodegradable and can improve the strength of a base resin that is already sustainable. These fillers are a great choice for environmentally conscious applications. | Natural organic fillers don’t enhance mechanical properties as much as glass or carbon, and they can affect the appearance of the part, as specks may show through the plastic. An intentional color choice is one solution to this. Natural organic fillers are also a newer option, so there are fewer base resin options available currently. |
Talc Filled Plastic | Because it doesn’t melt, talc, commonly known as baby powder, is often used in thick-walled parts to provide structure during the molding process. Talc helps maintain the integrity of the part during molding. | Talc fill does not enhance mechanical properties beyond a slight increase in rigidity. |
Real-World Applications of Glass Filled Plastic
GFP’s are widely used in various industries due to its enhanced properties:
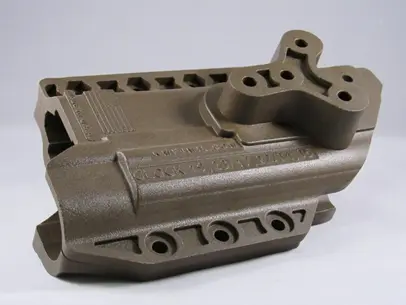
Military-Grade Parts: Many military-grade components utilize glass filled plastic to ensure durability and strength. An example from our portfolio includes a holster made from impact-modified nylon filled with 15% glass fiber. This part is designed to withstand heavy use, offering impact resistance and toughness.
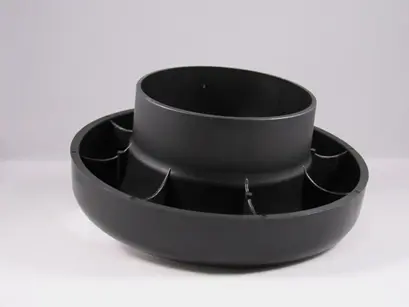
High-Stress Parts: GFP’s provides the necessary strength for components like automotive velocity stacks, which are subject to high stress.
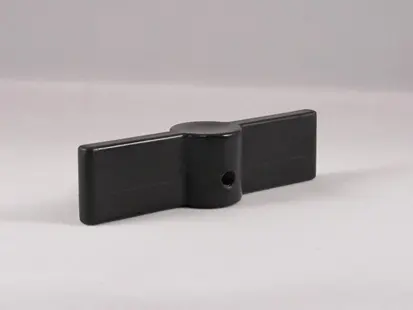
Thick Parts: For thick-walled parts, GFP’s helps reduce sink.
Let IMS Injection Mold Your Custom Parts
Glass-filled plastic is yet another way that we at IMS can customize your injection-molded parts to meet your needs and specifications. It offers a robust solution for applications requiring enhanced mechanical properties, chemical resistance, and long-term durability. While it does come with some challenges, such as increased brittleness and potential warpage, our engineers mitigate these through thoughtful design and engineering. Partner with IMS today to bring your vision to life.