Whether you need a single plastic prototype or millions of plastic parts, IMS has the technology and experience to manufacture any volume of quality plastic products.
At IMS, we take a holistic approach to each project. We listen to your vision, what kind of form and function you need in a part and the anticipated volume of your manufacturing project. Our engineers make suggestions in regard to manufacturing process, assembly, tooling, and plastic material based on your volume requirements. Whether you need five plastic parts or 5 million, our plastic injection molding company is here to guide you every step of the way.
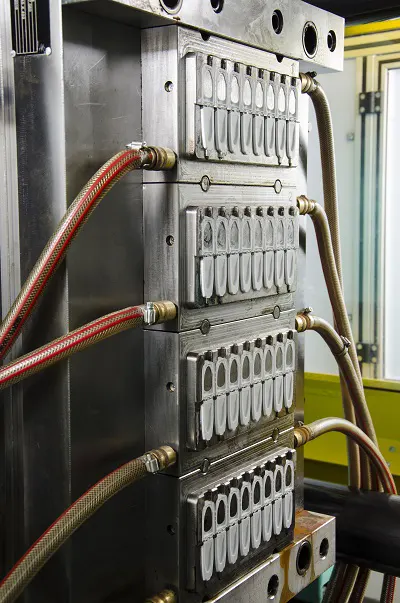
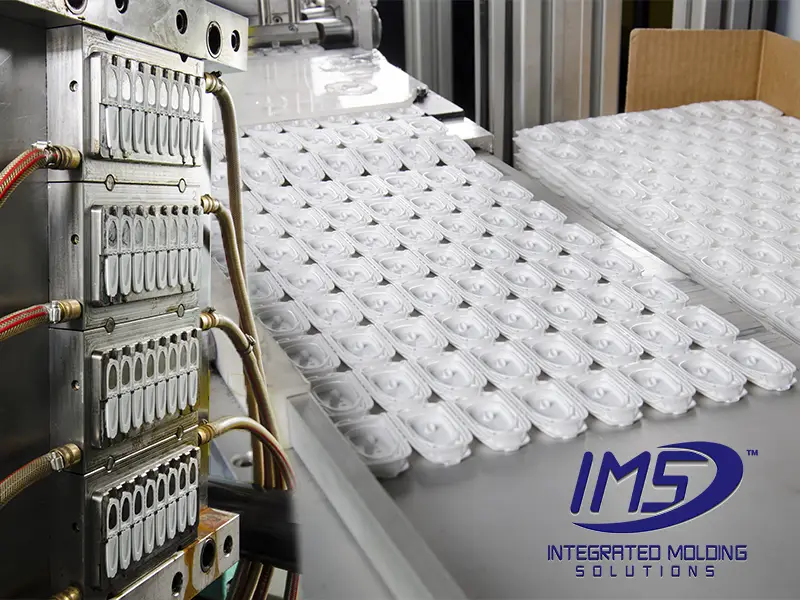
Low Volume 3D Printing
On the lowest end of scalability, we offer FDM 3D printing and PolyJet 3D printing. IMS engineers are experts in low volume manufacturing and will offer guidance on which of these two options is best for your project.
People Also Ask
What is plastic injection molding?
Whether you need five plastic parts or 5 million, our plastic injection molding company is here to guide you every step of the way. A low volume plastic injection mold is categorized as a Class 104 or Class 105 tool.
Why chose IMS for plastic injection molding?
This question is addressed in the article above.
Where can I go to get a quick quote?
This question is addressed in the article above.
FDM 3D Printing
FDM 3D printing is one of our areas of expertise. This rapid-prototyping option is cost-effective and has the advantage of a wide range of material options, including TPU, ABS, PLA, HIPS, and Nylon (Polyamide or PA). This allows us to closely replicate an injection molding material if the part is a prototype for a future injection molding run. While FDM 3D printing has the aesthetic disadvantage of layer lines, the functionality of the parts comes close to that of parts made by injection molding. FDM 3D printing is ideal for single parts to dozens of parts.
PolyJet Printing
PolyJet printing offers more precise, accurate surface conditions than FDM 3D printing. While PolyJet has a narrower range of material options than FDM, it still has a wide breadth of material performance availability. With PolyJet technology, we can replicate more rigid materials, more flexible materials, and just about everything in between. PolyJet 3D Printers can also print a plastic part in any shape with very few geometric restrictions.
Low Volume Injection Molding
For short run injection molding requiring part volume between 200 and a few thousand, IMS engineers design a lower volume injection mold out of softer steel or aluminum. Aluminum molds make tooling significantly more cost-effective while still guaranteeing that the tool has enough life for the entire job. Low volume tooling has low cavitation, with only one or two cavities per plastic mold. A low volume plastic injection mold is categorized as a Class 104 or Class 105 tool. With low or high volume injection molding, there is a broad range of plastic material options for your molded part.
Printed Tooling
In some scenarios for part volumes up to 200 pieces, printed tooling may be an option. Particularly for parts that are geometrically simple and smaller than 4 cubic inches, printed tooling can be a cost-effective option. Printed tooling is made using our PolyJet printer technology. IMS engineers will guide you on whether printed tooling or 3D printing is the best choice for low volume production of your specific product.
For low volume molding, our engineering team focuses on simplifying the tool so tooling cost per part remains as low as possible.
We also focus on simplifying assembly processes to ensure that post-process services aren’t negating cost-effectiveness. Lastly, we use DME MUD inserts for lower volume tooling. This universal mount system allows us to use less steel and fewer off-the-shelf components to build the mold, saving you significant money on tooling costs.
High Volume Injection Molding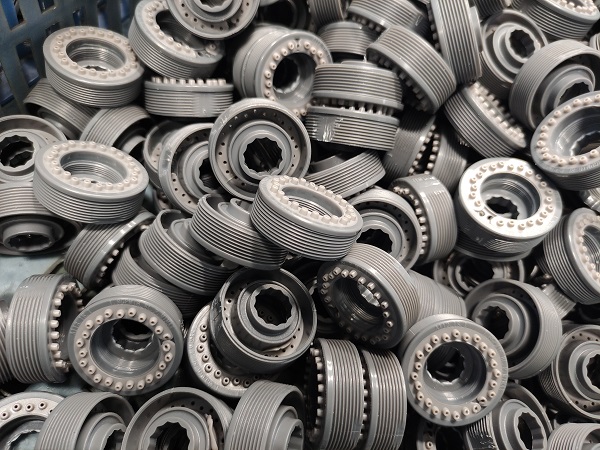
If you need thousands to millions of parts, IMS designs a Class 101, Class 102, or Class 103 steel tool. These tools are made with harder steel and are designed for longevity. If you need a more cost-effective metal option for tooling, we can also design an aluminum mold, If you need a more cost-effective metal option for tooling, we can also design an aluminum mold, and certain alloys of aluminum can reach similar shot counts to steel molds. High volume molds are built with higher cavitations, with anywhere from four to 32 cavities. For high volume molding, we use our larger injection molding machines and make more parts per shot, saving you time and money.
For high volume injection molding jobs, IMS engineers work with you to optimize the individual part design.
We also encourage the use of mechanical fastening features for high volume jobs. Using mechanical fastening features like snap fit joints saves you time, as you are not having to wait for parts to be screwed in or solvent-welded. If your project is not only high volume but also long lasting (e.g., you need 300,000 parts per month every month for a year or more), we can also build multiple tools to run simultaneously.
As part of our cutting-edge injection molding service, IMS invests in new technology to streamline our plastic part manufacturing process.
Investing in new technology allows us to continue delivering high volume production of quality plastic parts on time. Our engineers also develop automation techniques for the injection molding process so we are able to produce more plastic consumer products with lower labor costs. It is no longer more cost-effective to outsource high volume jobs overseas. IMS is experienced, qualified, and capable of delivering high quality parts for high volume jobs right here in the United States.
IMS offers bespoke solutions for high and low volume plastic injection molding. Contact us today to get started.
Whether you are a corporate client who needs millions of injection molded parts for use in the automotive industry or an entrepreneur who needs a prototype for your startup, IMS is here for you. We pride ourselves on listening to exactly what you need in a part and figuring out the best way to do it. We have scalability and decades of experience with both low and high volume jobs and are a well-regarded supplier to small businesses and large corporations alike. Check out our Resources Page for more information, or give us a call so we can answer any questions directly.