Emerging Biodegradable Plastic Materials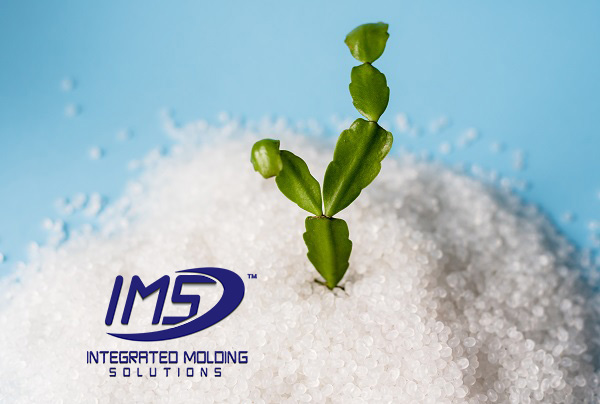
The global movement towards sustainability has spurred innovation in various industries, including manufacturing. Traditional plastics have long been a concern due to their environmental impact, leading to the development of biodegradable alternatives. In both injection molding and 3D printing, the adoption of plastic biodegradable materials is gaining traction as businesses and consumers alike seek eco-friendly plastic solutions. This article explores the evolution, advantages, and applications of biodegradable plastics in the realms of injection molding and 3D printing.
Understanding Biodegradable Plastics
Biodegradable plastics are derived from renewable resources such as corn starch, sugarcane, or other plant-based materials. Unlike conventional plastics, which persist in the environment for hundreds of years, biodegradable plastics break down more rapidly through the action of microorganisms, turning into natural byproducts like water, carbon dioxide, and biomass.
People Also Ask
What is plastic injection molding?
In both injection molding and 3D printing, the adoption of plastic biodegradable materials is gaining traction as businesses and consumers alike seek eco-friendly plastic solutions.
Why chose IMS for plastic injection molding?
This question is addressed in the article above.
Where can I go to get a quick quote?
This question is addressed in the article above.
Evolution of Biodegradable Materials
The journey towards sustainable plastics in manufacturing began as a response to the environmental repercussions of conventional plastics. Early biodegradable plastics faced challenges such as limited strength, flexibility, and higher production costs. However, advancements in material science and technology have led to the creation of biodegradable polymers that rival the performance of traditional plastics.
Advantages of Biodegradable Plastics in Injection Molding and 3D Printing
Environmental Impact: The most significant advantage of biodegradable plastics is their reduced environmental footprint. These materials decompose naturally, minimizing the long-term pollution associated with traditional plastics.
Renewable Resources: Biodegradable plastics often utilize renewable resources, contributing to a more sustainable and circular economy. This contrasts with conventional plastics, which are derived from finite fossil fuels.
Diverse Applications: Biodegradable materials are suitable for a wide range of applications, including packaging, disposable cutlery, medical devices, and more. In injection molding and 3D printing, these materials offer versatility in creating environmentally friendly products.
Reduced Dependency on Petroleum: Traditional plastics are largely derived from petroleum, a non-renewable resource. Biodegradable plastics, sourced from plants, reduce dependency on finite fossil fuels.
Enhanced Technology Compatibility: Biodegradable plastics have become increasingly compatible with injection molding and 3D printing technologies. Manufacturers can seamlessly integrate these materials into their existing processes.
Consumer Demand and Reputation: As environmental consciousness grows among consumers, there is a rising demand for products made from sustainable materials. Using biodegradable plastics in manufacturing can enhance a company’s reputation and appeal to eco-conscious consumers.
Applications in Injection Molding
Biodegradable plastics have found a significant application in injection molding, a process widely used for mass production of plastic parts. The adaptability of these materials makes them suitable for producing various items, including:
Packaging Materials: Biodegradable plastics are used to manufacture environmentally friendly packaging for food, beverages, and consumer goods.
Disposable Cutlery and Tableware: Injection molding enables the production of biodegradable forks, spoons, and plates, offering a sustainable alternative to single-use plastic.
Medical Devices: Biodegradable plastics are gaining acceptance in the medical industry, particularly for single-use items like surgical tools and disposable medical devices.
Consumer Goods: From phone cases to household items, injection-molded biodegradable plastics cater to a range of consumer goods.
Applications in 3D Printing
Biodegradable materials have also made their mark in the realm of 3D printing, also known as additive manufacturing. This technology allows for the creation of intricate designs and customized products. Biodegradable plastics are employed in 3D printing for:
3d Printing Prototyping: Manufacturers use biodegradable materials for rapid prototyping, allowing them to test designs without long-term environmental impact.
Customized Plastic Products: 3D printing with biodegradable plastics enables the creation of personalized items such as phone cases, fashion accessories, and even custom packaging.
Educational Models: In educational settings, 3D printing with biodegradable materials is used to create models and prototypes, providing a hands-on learning experience.
Architectural Models: Architects use 3D printing with biodegradable materials to create detailed architectural models with precision and sustainability.
Challenges and Future Outlook
The future outlook for biodegradable plastics in manufacturing is optimistic. Increased awareness of environmental issues and regulatory support for sustainable practices are driving the industry towards embracing eco-friendly alternatives. As technology continues to advance, the performance and cost-effectiveness of biodegradable plastics in injection molding and 3D printing are expected to improve, further promoting their widespread adoption.
The integration of biodegradable plastics into injection molding and 3D printing represents a significant step towards creating a more sustainable and environmentally conscious manufacturing industry. As businesses and consumers increasingly prioritize eco-friendly practices, the demand for biodegradable materials is set to grow. The versatility, renewable sourcing, and reduced environmental impact of these materials position them as crucial players in the ongoing quest for a greener future in the world of plastic manufacturing.
Plastic Manufacturing Experts Dedicated to Advancing Biodegradable Materials
Integrated Molding Solution’s team of plastic manufacturing experts offers a wealth of plastic industry expereince and knowledge in plastic material selection as well as the diverse options of biodegradable materials available for plastic manufacturing. We provide invaluable design insights and recommendations tailored to meet your plastic product’s specific needs. Partnering with IMS ensures not only the selection of the most suitable biodegradable material but also a conscientious approach towards environmentally friendly manufacturing. We strive to merge innovation with sustainability, enabling your product to embrace biodegradable materials without compromising on quality or performance. Collaborate with Integrated Molding Solutions to make informed choices that not only elevate your product but also contribute positively to our environment. Contact us Today!