Grow Your Business And Consider Metal to Plastic Conversion
Businesses are constantly seeking innovative solutions to enhance efficiency, reduce costs, and improve product performance. A significant trend in recent years is the shift from traditional metal products to plastic alternatives. This transformation, driven by advancements in materials science and manufacturing technologies, is not just a cost-cutting measure but a strategic move towards achieving lighter, more sustainable, and versatile products. In this article, we will explore the process of converting metal products to plastic, the advantages it offers, and the industries where this transition is making a substantial impact.
Advantages of Converting to Plastic
Weight Reduction: Heavier is not always better or stronger. Many plastic materials have a higher strength-to-weight ratio than aluminum or steel. With the right product design, you can manufacture the desired strength with many plastic alternatives.
Another primary advantage of converting metal products to plastic is the significant reduction in weight. Plastics are inherently lighter than metals, making them ideal for applications where weight is a critical factor, such as automotive and aerospace components. Converting to plastic can reduce weight without sacrificing strength, leading to less expensive shipping and decreasing the carbon footprint and impact on the environment. Additionally, the lighter weight of plastic products contributes to fuel efficiency in transportation, further reducing the overall carbon footprint.
Manufacturing Cost Savings: Plastic materials are often more cost-effective than metals, both in terms of raw material costs and production expenses. Most metal manufacturing methods, besides possibly stamping, don’t have the cycle time or production throughputs that injection molding can offer. The reduced weight also contributes to cost savings in transportation and logistics.
Further cost savings can be found by the reduction of scrap or plastic waste. With plastic, the extra raw material can be easily recycled and brought back into production. Whereas metal shavings are much harder to recycle back into production.
Plastic Material Flexibility: Plastic materials are much easier to change or adjust than metal materials at the manufacturing stage. Changing the metal can greatly impact the manufacturing method and the plastic part design. Once the injection mold is built, it is easier to adjust and change plastic materials without needing to change the design. There are also more plastic material options, than metal material options for production. The number of materials to choose from, even just base resins is outstanding. From nylons to polypropylenes, to blends like PC/ABS, there are so many different plastic material choices, and that number multiplies when you consider additives and fillers.
Manufacturing Design Flexibility: Plastic’s versatility allows for intricate and complex designs that may be challenging or costly to achieve with metal. Optimizing your product design for converting to plastic, will give you a wide range of cosmetic choices. Molds can be designed to have different textures and surface finishes applied, so the parts have a different texture, and surface finish, compared to metal parts. Generally, with metal components, you’re limited to coatings, machining, finishes, grinding, or polishing. But with plastic injection molding, we can design in a specific texture, like a wood or leather grain texture can be put into the tool so all the parts have that texture or surface finish.
Plastic injection molding can achieve tight tolerance requirements again and again. With machining metal products, if you take a block of aluminum and turn it into a part, every toolpath has tolerances we have to factor in. However, for injection molding manufacturing, once the mold is produced, your tolerances are set with little room for error outside of the material. This leads to improved QC and QA allowing a more efficient process to ensure precision. Once the mold is designed, the complexity won’t impact cycle time as much as it can impact cycle time for machining metal.
Another advantage of injection molding is you can eliminate secondary operations that you would generally need in something that’s being machined out of metals. This is because you can design features to be directly tooled directly into an injection molded part. Hinges, for example, on a metal part you would have to have a two-piece mechanical component that acts as a hinge. Other features injection molding allows us to design into the plastic product include latches, snap fittings, fasteners, labels, raised text, and more.
Corrosion Resistance: Unlike metals, many plastics are naturally resistant to corrosion. This makes plastic products an excellent choice for applications where exposure to harsh environments or corrosive substances is a concern.
Insulation Properties: Plastics offer superior insulation properties compared to metals. This is advantageous in applications where electrical insulation or thermal insulation is crucial.
The Metal to Plastic Conversion Process
Converting metal products to plastic involves a systematic and strategic approach that encompasses material selection, design modification, and adaptation of manufacturing processes. The key steps in this conversion process include:
Plastic Material Selection: Choosing the right plastic material is crucial for plastic manufacturing. Engineers and designers consider factors such as mechanical properties, thermal characteristics, and chemical resistance to ensure that the selected plastic can meet or exceed the performance of the original metal.
Design Modification: The transition from metal to plastic often requires adjustments to the product design. This includes optimizing part geometries, adjusting wall thickness, and incorporating features that leverage the unique properties of plastics, such as living hinges or snap-fit features.
Tooling and Mold Design: Precision in mold design is essential to ensure that the plastic material is injected or molded accurately, resulting in a high-quality final product. Investing in professional tooling is very important to ensure the quality and precision of injection molded plastic components.
Manufacturing Process Adaptation: The manufacturing process itself may need to be adapted to accommodate plastic materials. This can involve changes in temperature control, injection molding parameters, and post-processing techniques.
Testing and Validation: Rigorous testing and validation are essential to ensure that the converted plastic product meets or exceeds the performance standards set by the original metal product. This includes mechanical testing, thermal analysis, and validation against industry-specific standards.
Industries Embracing Converting To Plastic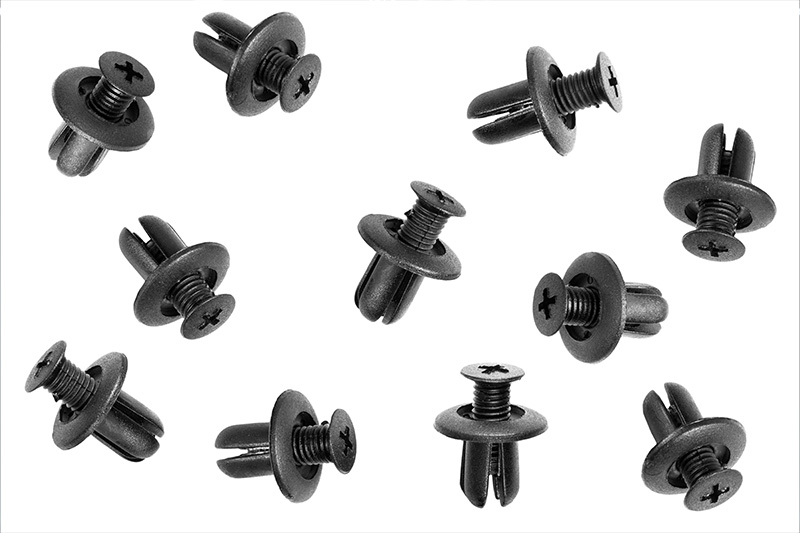
Automotive: The automotive industry has been a pioneer in converting metal components to plastic. From interior components to under-the-hood applications, plastics are increasingly replacing traditional metals, contributing to fuel efficiency and reducing vehicle weight.
Aerospace: The aerospace sector is leveraging the benefits of plastic conversion to reduce the weight of aircraft components without compromising on strength and durability.
Consumer Electronics: The consumer electronics industry is adopting plastic conversion for casings, frames, and internal components. This allows for sleek designs, reduced weight, and improved durability.
Medical Devices: Plastic’s biocompatibility and flexibility make it an ideal choice for various medical devices. The transition to plastic has enabled the production of lighter, more ergonomic, and cost-effective medical equipment.
Packaging: In the packaging industry, the transition from metal to plastic has led to the development of lightweight, durable, and environmentally friendly packaging solutions.
Construction: Certain construction applications, such as pipes, panels, and roofing materials, are now incorporating plastic components for their durability, corrosion resistance, and ease of installation.
The conversion of metal products to plastic marks a paradigm shift in modern manufacturing, driven by the pursuit of lightweight, cost-effective manufacturing.
At Integrated Molding Solutions, our expertise in injection molding goes beyond production; it encompasses a comprehensive understanding of the entire conversion process, taking a metal component to a plastic component. With a dedicated team of professionals and vast experience in material science, plastic part design optimization, and cost-efficient additive manufacturing methodologies, we will guide you through every step of the transition. We help ensure that your conversion to plastic parts from the metal counterpart is seamless, cost-effective, and optimized for superior performance. Trust IMS to assist you in the entire injection molding process, ensuring that your plastic part not only meets but exceeds your expectations. Trust Integrated Molding Solutions to guide you on how best to convert your parts and products from metal to plastic.