Tooling
Detailed Tooling for Injection Molding
The tooling step in the plastic additive manufacturing process is critical to ensure your plastic part meets your expectations and specifications. Furthermore, proper tooling improves repeatability and consistency in manufacturing mass production parts. Without adequate tooling, your injection molding manufacturing process will fail.
The main goal of plastic injection molding tooling is to obtain a solidly designed mold that retains reproducible results throughout high volume production. Detailed tooling creates the highest quality parts with consistently tight tolerances. Tooling design services, as well as the material choices, affect tolerances. Therefore, complex patterns require precision accuracy in the tooling process to maintain true measurements.
People Also Ask
What is plastic injection molding?
ToolingDetailed Tooling for Injection MoldingThe tooling step in the plastic additive manufacturing process is critical to ensure your plastic part meets your expectations and specifications. The main goal of plastic injection molding tooling is to obtain a solidly designed mold that retains reproducible results throughout high volume production.
Why chose IMS for plastic injection molding?
This question is addressed in the article above.
Where can I go to get a quick quote?
This question is addressed in the article above.
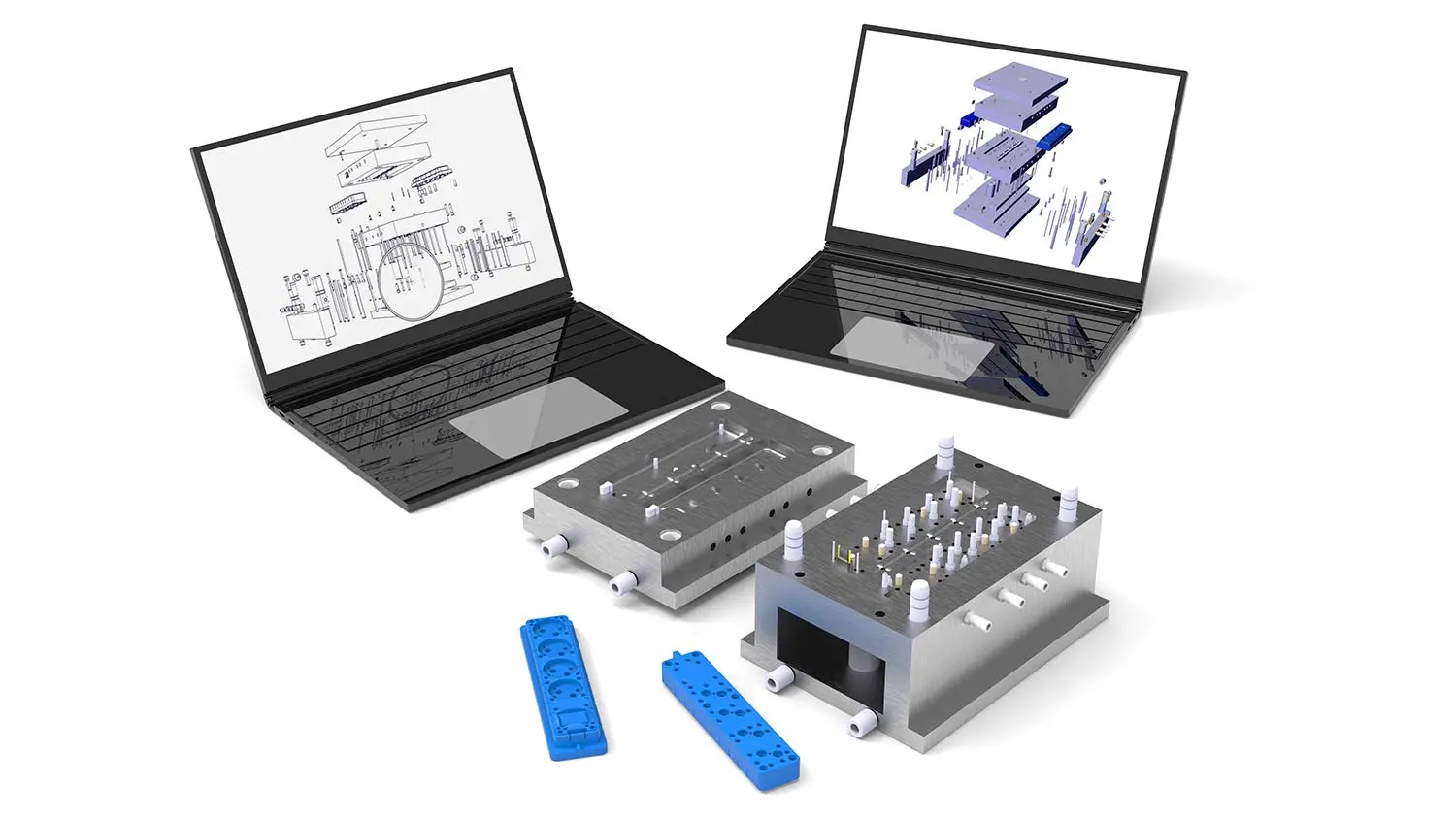
IMS Injection Molding Tooling Services
IMS offers a wide range of tooling, both foreign and domestic. Our full-service manufacturing includes fabricating fixtures and jigs, designing molds, and tool repairs. A fixture or jig are the items tooling needs to hold, clamp, align, bend, drill, and manipulate your mold component. The internal tooling department utilizes lathes, milling machines, and precision cutting equipment to create the highest quality mold. Additionally, we perform preventative maintenance and rigorous inspections to ensure all parts meet quality standards and project specifications.
IMS 3D printing often provides clients with a prototype before the tooling process begins. Our design services furnish a prototype so clients can see an approximation of the finished product in hand. Having a 3D prototype helps our clients understand if the finished product will fit their needs as intended. Otherwise, modifications will happen before beginning the tooling phase.
Our Advanced Plastics Manufacturer Knowledge
Getting the most out of your tooling phase starts by choosing the right manufacturer who has the experience and know-how to successfully tool. Also, working with production partners for professional tooling will be helpful when the part requires more intricate mold patterns. IMS helps you find the perfect fit to get the process started. You can rest assured that we’ll find the correct tooling answers and get your project underway, right away. Starting with expert plastic manufacturing advice will ensure many important design decisions are accounted for before tooling is finished. It is crucial to catch and make any corrective actions before the mold leaves the tool maker, to avoid costly expenses. Our skilled, knowledgeable staff is ready to advise on optimizing your tooling design services to reach optimal results.
Knowing the Tooling Risk Factors
We need to be fully aware of our client’s needs, from design to final usage in our business. Plastics engineering is a delicate process. There are numerous factors to consider when injection molding precision parts. IMS veterans in the plastics industry identify risk factors and outcomes before the project begins. These skilled professionals identify and prevent common mishaps, oversights, and possibly catastrophic results such as warping, excess shrinking, or mold failure.
Temperatures, melting point, flow rate, and cooling are a few of the many risks associated with plastic injection molding. Our experts determine the best avenue in the process to avoid common risks and identify potential issues within each project scope. Then, we develop the best possible solutions.
Tooling Requires Materials Too
For cost-effective solutions, your fabricator must consider the tooling materials as well as the proper project material. Multiple cost-effective options are dependent on your plastic part requirements. For instance, aluminum molds, mud inserts, or printed inserts are a few available options to reduce tooling costs.
Another option may be a family tool mold. A family casting is a mold that holds multiple parts in the same mold at one time. Each option carries with it specific advantages and disadvantages. Choosing suitable materials is critical to the tooling process to hit the client’s desired results in the most efficient and cost-effective way.
IMS remains flexible throughout the manufacturing process.
In any situation that may arise, we are continually professional and ready to serve our clients in their best interests. Many clients choose our knowledgeable staff to help guide them in the right direction. Experienced artisans guide you away from generic design choices in favor of productivity options that provide quality and efficiency. Working closely with the IMS team, together, we optimize design concepts.
We’ll modify specifications to make precision injection molds that produce efficiency in functionality and aesthetically pleasing finished parts. When you work with IMS, you’ll know that your components exceed all expectations before we deliver to your door. We produce nothing less than exceptional every time.
Getting precision tooling accurate is critical to the overall production’s success.
Tooling is the most laborious part of the manufacturing process because the project’s outcome depends on a precision-manufactured mold. The more geometrically complex the design, the more elaborate tooling is needed to reach the desired results.
Why do we need tooling?
Stop and take a moment to look at all the products surrounding us. Most products consist of multiple parts assembled together. Injection molding fabricates plastic parts by melting plastic materials and injecting them into injection molds. Tooling uses complex tools and machines to design and test the molds. Yet, creating the perfect mold is difficult.
Your mold is the key to getting the ideal product instead of a merely functional product. The tool design process is the core to making perfect components you can stand behind. So, when you need a plastic part, tooling is the critical step in plastic manufacturing that takes your design patterns to a physical possibility.
The tooling process shapes the mold to the exact part’s specifications.
The mold often begins as a metal bar. Metal is commonly used for the mold because metals withstand repeated high pressure during the injection process. Yet, molds may also use some other plastics and materials. The tooling process forms the metal or other material into a mold base. The raw material goes into a milling machine that meticulously shaves the bars to the correct dimensions. CNC machining cuts it to a technically accurate design according to the blueprints and schematics. A tooled mold can be as detailed as 0.001 variances. The process of getting the molds, fixtures, and jigs ready for manufacturing is known as tooling.
The Process After Tooling
After tooling, the mold goes to the injection molding department. Here we inject molten plastic into the newly designed molds. After the mold is cooled, the plastic parts are ejected from the molds. Consider, when the injection process is complete additional services are applied as needed per the project specifics. In that case, you may need surface finishing options and various secondary operations such as painting, pad printing, heat staking, assembly, and packaging.
IMS has you covered if you need secondary services to complete your plastic part. Get all your injection molding services done with one trusted manufacturer – Integrated Molding Solutions.
Cooling Process
Cooling is a critical step to injection molding. Complex parts that need to maintain tight tolerances are at risk. For example, scientific tooling determines which variables to consider for reduced shrink during the cooling phase. Experienced professionals will design molds in such a way to provide adequate cooling. Your IMS expert knows the correct number of cavities needed for proper cooling in the mold. Also, they know the right material for the project, and which cooling method is best for that material. Likewise, the mold cooling process is also critical for determining surface finishing options.
What is tooling?
Tooling is designing the right equipment for the manufacturing process. In plastic injection molding, this means cutting and shaping the mold and any necessary jigs and fixtures used to manufacture all of your plastic parts. Producing these tooling components gives the product its final shape.
Tooling requires excellent attention to detail and planning. Engineers carefully design and measure each mold cavity to meet exact project specifications and provide adequate cooling. The injection molding process is made faster by professional-quality tooling.
CAD Printing Design
CAD printing is a computer-aided design that provides detailed specs of the part. CAD software designs the piece in 3D space, optimizing it for manufacturing. After, plastic manufacturers use CAD to develop the 3D printing sample and tool the mold.
The computer-aided design keeps tight tolerances during the tolling and manufacturing process. Computer designs speed up the creation and blueprinting. Also, it ensures the completed part upholds exact measurements. Computer designs are naturally more detailed and precise than hand-drawn design specs.
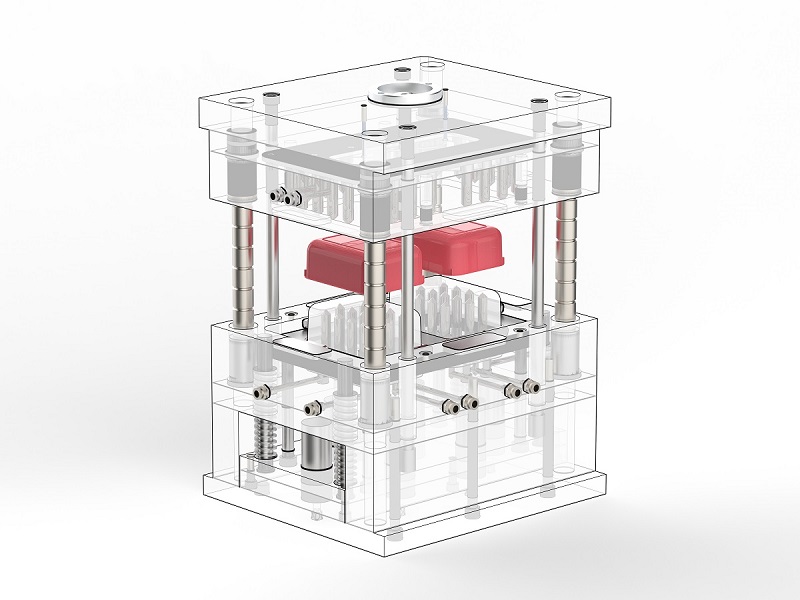