Injection Molding Draft Angle 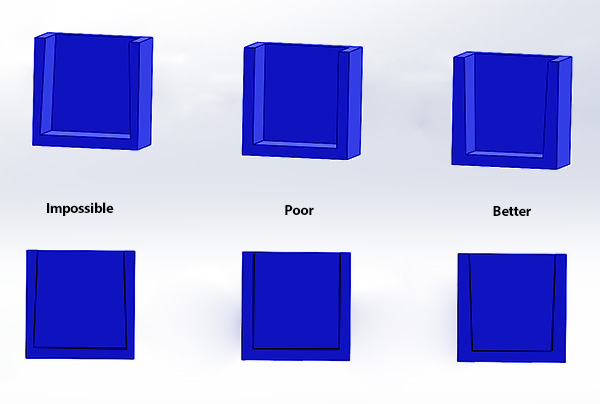
One of the often overlooked but crucial aspects of precision injection molding is the draft angle. Draft angle, sometimes referred to as draft or taper, is a design feature that influences the success of the molding process and the quality of the final product. In this article, we will explore the importance of draft angles in injection molding and how they impact the design, product development, molding, and functionality of the plastic product.
What is Draft Angle?
Draft angle is the degree of taper or slope applied to the vertical faces of a plastic part or plastic product manufactured by injection molding. In plastic injection molding, it is crucial for a smooth ejection of the plastic parts from the mold cavity. Without an appropriate draft angle, the part may get stuck in the mold or sustain damage during ejection, leading to defects and production delays.
People Also Ask
What is plastic injection molding?
In plastic injection molding, it is crucial for a smooth ejection of the plastic parts from the mold cavity. During the injection molding process, molten plastic is injected into the mold, where it cools and solidifies.
Why chose IMS for plastic injection molding?
This question is addressed in the article above.
Where can I go to get a quick quote?
This question is addressed in the article above.
Draft angles typically are measured in degrees and are applied to the vertical surfaces of the part. The specific angle required depends on several factors, including the type of material being used, the complexity of the part’s geometry, and the characteristics of the molding process.
Draft angles are an often underestimated but essential element of successful injection molding.
Just knowing when to use a larger draft angle vs a smaller draft angle can enhance the quality and efficiency of your injection molding processes and achieve superior results in the production of plastic components. Ignoring the importance of draft angles can lead to production delays, increased costs, and lower-quality parts.
Injection Molding Draft Angle Ensures Easy Ejection
The primary purpose of a draft angle is to facilitate the easy and smooth removal of the molded part from the mold cavity. During the injection molding process, molten plastic is injected into the mold, where it cools and solidifies. Without a draft angle, the part can create a vacuum-like effect, causing it to stick to the mold’s vertical walls. This can result in damage to the part or the mold itself when it is forced to eject.
By incorporating the appropriate draft angle, the part can be released from the mold with minimal resistance, reducing the risk of defects and ensuring a faster and more efficient production process.
Minimizing Cosmetic and Structural Defects
Draft angles also play a significant role in preventing cosmetic and structural defects when injection molding plastic parts. Without proper draft angles, several issues can arise:
Scratching and Scuffing: Insufficient draft can cause friction between the part and the mold, leading to scratches, scuffs, and blemishes on the part’s surface.
Warpage: Inadequate draft angles can result in warping, as the part may experience uneven cooling and stress during ejection.
Design Considerations for Draft Angle Injection Molding
When designing parts for injection molding, it’s essential to consider draft angles from the outset. Here are some key considerations for determining the proper draft angle:
Consultation with Mold Designers: Collaborate closely with mold designers and manufacturers to determine the optimal draft angles for your specific part and material.
Material Characteristics: Different plastic materials may require different draft angles due to variations in shrinkage rates and flow properties.
Part Geometry: Complex or intricate plastic parts may require more generous draft angles to ensure proper mold filling and ejection.
Surface Finish: The level of texture or surface finish required on a part affects the amount of draft needed. Deeper/more aggressive textures require more draft.
Tolerances: Account for any required tolerances in your part design, as draft angles can influence the final dimensions of the injection molded part.
The Benefit of Expert Plastic Manufacturers & Mold Makers
Collaborate with injection molding specialists like Integrated Molding Solutions, to ensure your plastic parts and mold design are done correctly. Through draft angle analysis, experts consider factors like draft direction, injection angles, mold release, and the impact of a textured surface, to incorporate into the product and plastic injection mold design. IMS will work with you to optimize your designs before you find defects in your finished product. Contact Integrated Molding Solutions, and let’s discuss your plastic product design or manufacturing process today!