How are plastic products made?
Making plastic products is a complex, multi-step process. Integrated Molding Solutions simplifies it. We are here to guide and advise you with fairness and decades of experience in the plastic injection molding process.
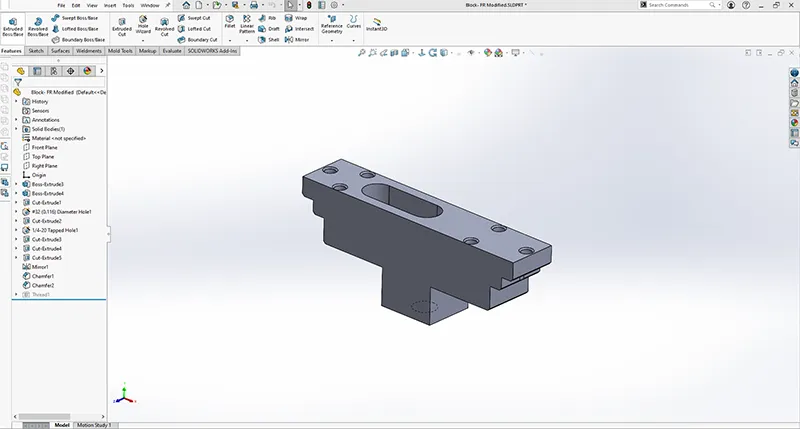
Beginning with design, material selection, and prototyping, we work with you to ensure your plastic parts are produced to meet any requirements in the most cost-effective way possible. We partner with a variety of trusted toolmakers to create tooling that meets your plastic mold needs. IMS experts quality check your plastic part samples, then we give those samples to you so you can perform your own quality checks before we enter production. We are equipped to produce any volume of your plastic parts and provide all post-production and secondary services. IMS is a one-stop shop for injection molded plastic parts.
People Also Ask
What is plastic injection molding?
We are here to guide and advise you with fairness and decades of experience in the plastic injection molding process. IMS is a one-stop shop for injection molded plastic parts.
Why chose IMS for plastic injection molding?
This question is addressed in the article above.
Where can I go to get a quick quote?
This question is addressed in the article above.
Integrated Molding Solutions’ experts guide you through every step of the injection molding process.
Step 1: Design
The plastic design process is collaborative and perhaps the most important of the injection molding processes. From material selection to moldability and prototyping, IMS works closely with you to identify the application requirements of the part. We take into account strength requirements, aesthetic preferences, and chemical-resistance needs.
IMS engineers are experts at ensuring functionality and moldability of the part. It is critical that the molded part functions as intended. During the plastic design phase, we also discuss the expected production volume of the part and timeframe for production.
Material Selection
In order to meet application requirements, the right material must be used for the job. There are hundreds of raw material and plastic resin options for plastic injection molding. Not all plastic functions in the same way, and IMS guides you toward the choice that is best for the specific part. After discussing the pros and cons of viable plastic material options, you are equipped to make the choice that is best for your budget and needs.
If sustainability is a priority for your business, IMS experts provide you with raw material options to meet sustainability requirements. You may have a material in mind already for your plastic part. In this case, IMS can use the exact material or find a comparable, more cost-effective alternative. Our goal is to help you create the part you want at the lowest possible cost. Further, we provide guidance on additive selections for materials. For example, some parts may require additives like flame retardants, color, or anti-static chemicals.
Moldability
The part must be designed in the simplest way that allows for moldability and cost-effectiveness in addition to desired form and function. Developing a repeatable process using an injection molding machine allows us to produce parts economically. We identify areas on a plastic part that need to be optimized or changed in order to be molded more easily. Our professional plastic designers make sure the part design avoids common pitfalls that affect the function, moldability, or aesthetics of the part. Our engineers have decades of experience simplifying customer designs in order to maintain functionality and compatibility with each plastic injection molding machine we use, while also ensuring the lowest possible costs for molding, tooling, and production.
Prototyping
Depending on your design needs and preferences, IMS can create custom digital models or CAD drawings for your part, or we can collaborate with outside design partners. Once we have the CAD files, we begin prototyping. Prototypes confirm that the plastic part design functions as intended.
plastic parts can be difficult to interpret or evaluate using digital renderings or CAD models alone. Prototypes, which are often created through 3D printing, allow you to get a feel for the part, test the part to make sure it functions properly, and present the part to investors. Based on feedback, IMS makes any necessary alterations to the design and re-prototypes until the design is exactly right in form, function, and moldability.
Design Changes
Part of the plastic design process for injection molding involves tweaking or changing the design to improve functionality and moldability. Changes during the design phase may be expected and incorporated into your quote. Partnering with IMS for your plastic needs ensures that any changes to your plastic part design or mold design are well thought out and implemented as early in the process as possible. Once the tooling or injection molds have been created, changes become much more expensive and time-consuming. IMS experts work diligently to make any necessary changes as early as possible.
Step 2: Tooling
IMS partners with a number of qualified, reputable toolmakers, both domestic and international. The toolmaker’s job is to design the mold into which melted plastic is injected to form your part. Adding simplicity and moldability to your part design pays off in this step. The simpler the part design, the more cost-effective tooling is. For parts that require complex design elements, IMS engineers provide guidance on tooling features like rotating or collapsible cores, slides, or lifters. We also use our expertise to find efficient ways of tooling, using Master Unit Die (MUD) bases or inserts, creating an aluminum mold instead of a steel mold, or using different grades of steel for steel tooling. We also take into consideration desired surface finishes and textures.
Once we know the volume of parts required, the material being used, the budget, and the desired lead time, IMS provides you with options for different toolmakers and helps you choose the appropriate injection mold class. Different classes of molds are appropriate for different jobs. For a job that requires millions of parts to be produced, a Class 101 mold is the correct choice. While a Class 101 mold is more expensive up front, it saves cost over time, particularly for jobs that require more than one run. The price per part decreases as the number of parts ordered increases. Once you have paid for the initial tooling, you can continue to use that to produce thousands to millions of parts.
Step 3: Quoting
By the end of the tooling stage, IMS provides you with an accurate and detailed quote. Our quotes include part numbers, part material, injection mold classification, mold cavity count, tooling cost, tooling lead time, tooling location, part weight, part set cost, and shipping costs including freight and duties if applicable. IMS quotes for different numbers of production volume so you can see how price per part decreases as production volume increases.
Toolmaker Collaboration
Placing a production order is a seamless process using the IMS Client Portal. Once you place an order, we work directly with the toolmaker to solidify the mold design. Our thorough communication with the toolmaker ensures mold compatibility with IMS injection molding machines and that the mold meets all project requirements. IMS keeps you updated throughout this manufacturing process so you stay in the know as your mold is being created. Your quote includes mold design and revisions.
The IMS team collaborates with the toolmaker throughout the toolmaking process. We confirm that the correct grade of steel is ordered and that the mold design is finalized to our high standards. Once the toolmakers begin constructing the mold, we supervise the rough machine passing as well as the fine machining or electrical discharge machining (EDM) to guarantee that the mold is created with accuracy. This collaboration during the tooling process sets IMS apart from our competitors.
Step 4: Sampling
Toolmaker Samples
At this stage, the tool is made and ready to produce your plastic part. We have the toolmaker run 10 to 20 samples and ship them to us to be evaluated. IMS engineers then perform internal quality control. We evaluate the samples to certify that they have been properly molded, that the material is working for the application, that there are no defects, and that the dimensions are correct. Once we have approved the samples, we send them to you so your business can perform its own qualification process. Once you sign off on the samples from the toolmaker, the mold is prepped for shipment. It is coated with anti-corrosives, packaged in a protective crate, and shipped to IMS.
IMS Samples
When IMS receives the mold, we are prepared with the material needed for the part so we can promptly run our own set of samples to evaluate. This sample run shows you exactly what you can expect when we produce your injection molded parts. It also allows our technicians to ensure that the injection unit is set to the correct injection speed and injection pressure and that all mold and process components are functioning properly for the specific plastic molding job.
Making modifications to the tooling at this stage is costly and time consuming, though not impossible if a major design change is requested. Easier to alter at this stage are material selection, packaging choices, and assembly options. It is important to note that this injection mold is owned by you, not by IMS. We use the mold to produce as many parts as you need, and store injection molds for future runs.
Step 5: Production and Post-Production
Once you are satisfied with the injection molded part samples, IMS begins production on your parts order. We pride ourselves on our quick production speed and injection molding cycle time. Plastic injection molded parts can often replace plastic parts made with other processes, such as CNC machining, at a fraction of the cost and in a fraction of the time. We are equipped to efficiently produce tens, hundreds, thousands, or millions of your parts. You can place more production orders at any time in the customer portal.
Post-Process Services
IMS offers a comprehensive range of post-production services. We provide all secondary assembly processes onsite, whether your parts need to be welded, bonded, tapped, or threaded. IMS artisans perform post-process part decoration as well, including painting, labeling, and over-molding. We also handle all of your part packaging needs. Integrated Molding Solutions is able to package the parts individually for retail or in bulk to be shipped directly to you. We are experienced with working within specific shipping parameters based on customer needs.
When you are ready to start the plastic injection molding process, contact IMS and let us simplify things.
We recognize that some customers may come to IMS with only a general part idea in mind, while others may already have a product design or functional prototype. Regardless of where you are in the manufacturing or design process, IMS is here for your plastic needs. Contact us today to start the injection molding process.