Understanding Reverse Engineering Parts
In plastic product manufacturing, reverse engineering parts allow the recreation of physical components or detailed drawings of initial prototypes. Unlike its digital counterpart prevalent in software engineering, reverse engineering of physical products involves dismantling parts and assemblies to uncover how they work. In this comprehensive guide, Integrated Molding Solutions shares our insight into plastic reverse engineering, exploring its methods, applications, and significance in plastic 3D printing and injection molding manufacturing.
Reverse engineering entails deconstructing objects to unveil their underlying design principles and functionality. This methodological approach is particularly valuable when access to original models, drawings, or technical specifications is limited or non-existent. By dissecting and scrutinizing each component, plastic engineers gain valuable insights into the intricacies of a product’s design and possible enhancements. Reverse Engineering parts can also be used to optimize part design or functionality. By understanding the product’s current wall thicknesses, draft angles, and inner workings, you can identify what is or isn’t necessary elements of the product’s design.
Methods of Reverse Engineering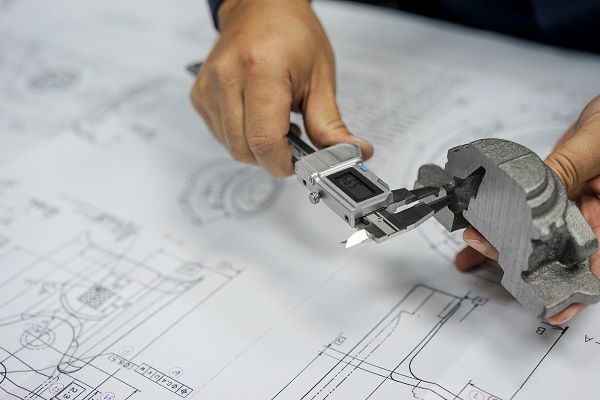
Reverse engineering encompasses a variety of methods and tools tailored to capture precise measurements and data. This is a vital step for precision injection molding and plastic manufacturing. There are many ways to reverse engineer products, from traditional hand-measuring tools like calipers and micrometers to sophisticated optical measuring equipment such as profile projectors and vision measuring machines. Furthermore, advancements in technology, including coordinate measuring machines (CMMs) and 3D scanning through LIDAR, provide even more accurate replications of complex geometries and unconventional shapes.
Understanding Plastic Part Design
Reverse engineering is not just merely replicating dimensions, but understanding the function and purpose behind each design feature. By determining the “why” behind certain design decisions, engineers can make informed decisions regarding potential improvements or optimizations of the product. This analysis ensures that reverse-engineered components align with the intended functionality and performance standards.
Applications for Reverse Engineering Plastic Parts
Reverse Engineering serves as a vital tool for replacing obsolete or discontinued parts, ensuring the longevity of mechanical products and equipment. Moreover, reverse engineering facilitates product improvement and innovation by identifying areas for enhancement and optimization. From automotive components to consumer electronics, reverse engineering plays a pivotal role in driving product evolution and technological advancement.
Reverse Engineering Parts for Plastic 3D Printing or Injection Molding
In the plastic manufacturing industry, reverse engineering plays a large role in streamlining production processes and enhancing product quality. Reverse engineering allows manufacturers to recreate intricate components with precision and ensures seamless integration within their assemblies. Furthermore, it assists the development from prototype to production, converting handmade or makeshift prototypes into manufacturable designs and drawings. Whether it’s injection molding or 3D printing, reverse engineering drives the plastic manufacturing process from concept to final product.
Legal and Ethical Considerations
While reverse engineering is a legitimate practice under U.S. law, it’s essential to follow legal and ethical processes responsibly. If the process doesn’t infringe upon existing patents or intellectual property rights, reverse engineering remains a practical method of innovation and problem-solving. However, you must exercise caution to ensure compliance with regulations and industry standards.
Reverse engineering stands as a large part of modern manufacturing practices. As technology continues to evolve, reverse engineering will only become more common, driving product creativity and optimization. With its numerous benefits and applications, reverse engineering remains a powerful tool for forward-thinking plastic manufacturers like Integrated Molding Solutions.